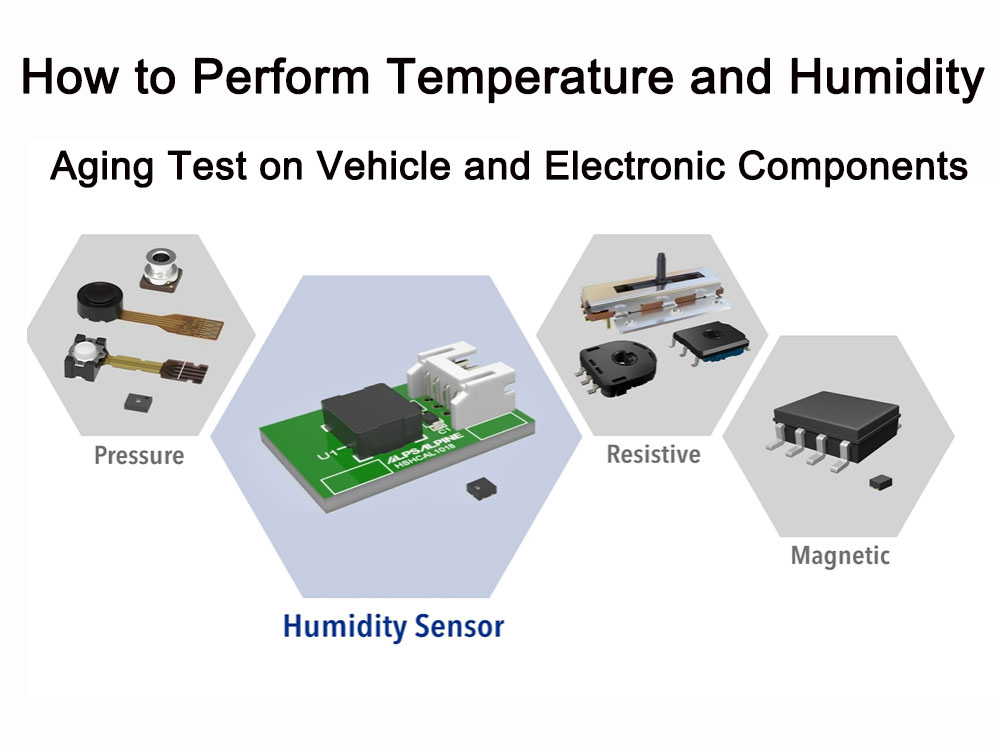
How to perform temperature and humidity aging test on vehicle and electronic components?
The temperature and humidity aging test of automotive and electronic components is an important method to evaluate the performance and reliability of electronic components under various temperature and humidity conditions.
The following are detailed test steps:
Electronic component test preparation
- Determine the purpose of the test: Clarify the goal of the test, whether it is to evaluate the temperature and humidity tolerance, performance stability, reliability or other related parameters of the component.
- Select test equipment: Select an appropriate temperature and humidity test chamber or aging chamber to ensure that it has temperature and humidity control capabilities, as well as appropriate volume and load capacity.
- Prepare samples: Select the electronic components to be tested and ensure that they comply with relevant standards and specifications. Prepare sufficient samples for repeated testing and analysis.
- Set test conditions: According to the purpose of the test and the characteristics of the components, set appropriate temperature and humidity conditions, such as temperature range, humidity range, temperature fluctuation range, humidity fluctuation range, etc.
- Develop a test plan: According to the test conditions and purposes, formulate a detailed test plan, including test cycle, data collection, analysis methods, etc.
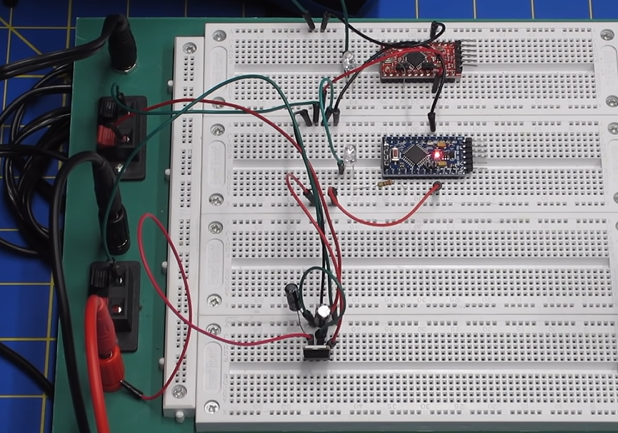
Electronic component sample installation and placement
- Clean the sample: Clean the selected electronic components to remove dirt and dust on the surface.
- Install the sample: Install the electronic components in an appropriate position in the test chamber, ensuring that they are kept at a certain distance from the test chamber wall to better control the temperature and humidity conditions.
- Arrange connecting wires: For testing needs, it may be necessary to arrange appropriate connecting wires in the test box to ensure the connection between the components and the test system.
Electronic component testing process
- Start the test: Set the temperature and humidity parameters of the test chamber and start the test program.
- Monitoring parameters: During the test process, key parameters such as temperature and humidity are continuously monitored to ensure that they meet the preset conditions.
- Data recording: Record the performance parameters, appearance changes and other information of electronic components according to the time intervals set in the test plan. These data will be used for subsequent analysis and evaluation.
- Check for abnormalities: During the test, pay close attention to the condition of the electronic components, and if any abnormalities are found, they should be recorded and dealt with in a timely manner.
- Complete the test: When the preset test period is reached, end the test and close the test chamber.
Electronic component data processing and analysis
- Data sorting: Organize the collected data into tables or graphics to facilitate subsequent analysis.
- Data analysis: According to the purpose of the test, perform statistical analysis on the data to evaluate the performance of electronic components under various temperature and humidity conditions.
- Reliability evaluation: Based on the data analysis results, the reliability of electronic components is evaluated, including life prediction, failure analysis, etc.
- Optimization suggestions: Based on the test results, put forward optimization suggestions for electronic components, such as improving design, improving manufacturing processes, etc.
Electronic components temperature and humidity aging report and summary writing
- Write a report: Organize the entire test process, data processing and analysis results into a report to clearly explain the performance of electronic components under temperature and humidity aging conditions.
- Summarize experience and lessons: Based on test results and data analysis, summarize experience and lessons, and propose improvement measures and suggestions.
- Report review and release: Review the report to ensure its accuracy and completeness. Then publish it to relevant people or institutions to provide them with valuable information and suggestions.
- Data archiving: Archive and save all documents, data and reports throughout the test process for subsequent review and use.
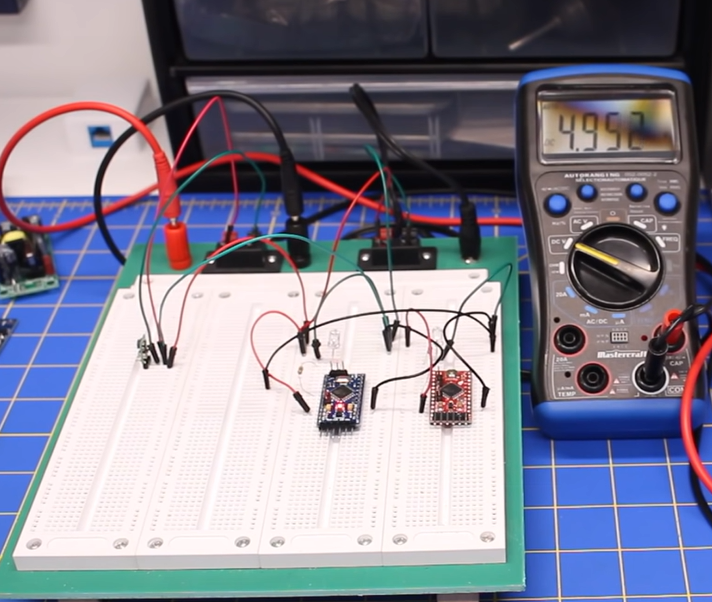
The above are the basic steps and requirements for temperature and humidity aging testing of automotive and electronic components. Since the temperature and humidity aging test is a complex process, actual operation may need to be adjusted and optimized according to specific conditions. Therefore, before conducting tests, you should fully understand the relevant standards and specification requirements, and have sufficient professional knowledge and experience.
After the test, how to perform subsequent maintenance on electronic components?
After the temperature and humidity aging test is completed, in order to ensure the long-term stability and reliability of electronic components, a series of maintenance measures are required. Here are some suggestions:
- Cleaning: Clean the electronic components after the test to remove dust, dirt and other impurities remaining on the surface. Use appropriate cleaners and tools to avoid damage to components.
- Check the appearance: Carefully check the appearance of the electronic components to ensure there is no obvious damage or abnormality, such as cracks, discoloration, ablation, etc. If there is any abnormality, it should be repaired or replaced in time.
- Test performance: Perform performance testing on electronic components to ensure their normal operation. Its performance status can be evaluated by testing its electrical parameters, functional characteristics, etc. If there are any abnormalities, adjustments or repairs should be made in time.
- Storage management: When storing electronic components, appropriate temperature and humidity conditions should be selected to avoid damage to components caused by excessively high or low temperature and humidity. At the same time, stored electronic components should be regularly inspected and refurbished to ensure that they are in good working order at all times.
- Maintenance records: Establish and maintain maintenance records for electronic components, and record in detail the status, maintenance history, replacement records and other information of each component. This helps track component performance changes and identify potential problems in a timely manner and deal with them.
- Preventive maintenance: Develop and implement a preventive maintenance plan and perform regular maintenance on electronic components. This includes cleaning, inspection, performance testing, etc. to ensure components are always in good working order.
Through the above measures, electronic components after testing can be effectively maintained and maintained to ensure their long-term stability and reliability. At the same time, it is also necessary to pay attention to the quality assurance and supply chain management of electronic components to ensure that the purchased electronic components have reliable quality and performance.
Frequently Asked Questions about Temperature and Humidity Aging Test of Automotive and Electronic Components
The vehicle and electronic components temperature and humidity aging testing machine is a professional equipment used to simulate temperature and humidity changes in the actual use environment and conduct aging tests on electronic components. The equipment provides high temperature, low temperature, high humidity, low humidity and other environmental conditions through technical means such as control systems, heating systems, humidification systems, refrigeration systems, and circulation systems to detect the performance and reliability of components and ensure the quality and stability of products. sex.
The working principle of the vehicle and electronic component temperature and humidity aging testing machine is to use temperature and humidity changes to simulate the actual use environment and conduct aging tests on electronic components. The required environmental conditions are set by the control system. The heating system, humidification system and refrigeration system control the temperature and humidity respectively. The circulation system ensures the air circulation in the test chamber.
The purpose of the temperature and humidity aging test is to evaluate the performance and reliability of electronic components under various temperature and humidity conditions. By simulating the temperature and humidity changes in the actual use environment, potential problems can be discovered in advance and optimized and improved to ensure the reliability of the product. sex and stability.
Temperature and humidity aging test is suitable for various electronic components, such as integrated circuits, transistors, capacitors, resistors, inductors, etc. At the same time, it is also suitable for other electronic products that need to detect temperature and humidity performance, such as automotive electronics, communication equipment, smart homes, etc.
The conditions for the temperature and humidity aging test should be set according to specific product standards and requirements. Generally speaking, the temperature should be between -55℃~+125℃, and the humidity should be between 0%~95%. The specific conditions should be determined according to the actual situation of the product. At the same time, the rate of change of temperature and humidity is also an important factor to consider. Too fast or too slow changes should be avoided from affecting the test results.
The time of the temperature and humidity aging test should be set according to specific product standards and requirements, and generally lasts from several hours to dozens of hours. In some cases, the test time may be hundreds or thousands of hours to fully simulate the temperature and humidity changes in the actual use environment.
In the temperature and humidity aging test, attention should be paid to controlling the test conditions, ensuring the accuracy and reliability of the data, avoiding damage to the samples, and maintaining the repeatability and traceability of the test process. At the same time, relevant safety regulations and operating procedures should be followed to ensure the safety of the test process.
The results of the temperature and humidity aging test should be concluded through data analysis and evaluation. Data analysis methods include statistical analysis, failure analysis, reliability assessment, etc. Through the collection, analysis and comparison of data, the performance and reliability levels of electronic components under various temperature and humidity conditions can be obtained.
Temperature and humidity aging tests of automotive and electronic components generally need to be conducted in professional laboratories or testing institutions. Before conducting the test, samples should be prepared, test conditions should be set, and a test plan should be formulated. During the test process, test conditions should be strictly controlled, sample status monitored, and data recorded. After the test is completed, the data should be organized and analyzed to draw conclusions.
In short, the temperature and humidity aging test is one of the important means to evaluate the performance and reliability of vehicle and electronic components.
By simulating temperature and humidity changes in the actual use environment, potential problems can be discovered in advance and optimized and improved to ensure product reliability and stability.
At the same time, it is also necessary to pay attention to issues such as test conditions, time, and safety to ensure the accuracy and reliability of test results.