Chip inductors is one of the commonly used components in electronic equipment. It is mainly used to store energy and implement functions such as signal filtering, coupling and transmission.
Improving the quality and reliability of chip inductors is of great significance to ensure the performance and stability of electronic equipment. The following is a detailed introduction on how to improve the quality and reliability of chip inductors:
Chip inductor material selection
- Core material: Choosing a core material with high magnetic permeability and low loss can improve the performance of the chip inductor. Commonly used magnetic core materials include manganese-zinc ferrite, nickel-zinc ferrite and iron powder core.
- Coil wire: The selection of coil wire is crucial to the quality and reliability of the inductor. Wires with high current carrying capacity, low DC resistance, high temperature resistance, corrosion resistance, etc. should be selected, such as copper wires, alloy wires, etc.
- Packaging materials: Packaging materials should have the characteristics of high temperature resistance, good insulation performance, and high mechanical strength to ensure the stability and reliability of the inductor. Commonly used packaging materials include epoxy resin, ceramics, plastics, etc.
Chip inductor manufacturing process
- Coil winding: During the coil winding process, the coils should be kept tight and even to avoid problems such as looseness and disconnection. At the same time, the number of turns and wire diameter of the coil should be controlled according to the design requirements to ensure the electrical performance of the inductor.
- Magnetic core assembly: During the assembly process of the magnetic core, the position of the magnetic core should be ensured to avoid tilting, loosening, etc. At the same time, the assembly pressure should be controlled to avoid damage or deformation of the magnetic core.
- Heat treatment process: The heat treatment process can improve the magnetic permeability of the magnetic core material and the mechanical strength of the coil wire. During the heat treatment process, the temperature and time should be controlled to avoid problems such as overheating and oxidation.
- Surface treatment process: Surface treatment process can improve the corrosion resistance and aesthetics of the inductor. Commonly used surface treatment processes include gold plating, silver plating, plastic spraying, etc.
Optimization of chip inductor structure
- Optimize the coil structure: By optimizing the coil structure, the DC resistance of the coil can be reduced and the heating performance and reliability of the inductor can be improved. For example, methods such as winding multiple strands in parallel and increasing the cross-sectional area of the coil are used.
- Optimize the magnetic core structure: By optimizing the magnetic core structure, the magnetic permeability of the magnetic core can be increased, the magnetic loss and heat loss can be reduced, thereby improving the performance and reliability of the inductor. For example, methods such as using high magnetic permeability core materials and reducing the cross-sectional area of the core are used.
- Optimize the packaging structure: By optimizing the packaging structure, the mechanical strength and stability of the inductor can be improved, thereby improving its reliability. For example, methods such as using reinforcing ribs and increasing package thickness are used.
Chip inductor quality control
- Strictly control material quality: Conduct quality inspections and tests on purchased materials to ensure that the quality of the materials meets requirements. At the same time, material quality files are established to track and control the quality of materials.
- Strengthen manufacturing process control: Develop strict manufacturing process and quality control standards, and monitor and record the entire manufacturing process. Timely discover and solve problems that arise during the manufacturing process to ensure product quality and reliability.
- Finished product inspection and testing: Conduct comprehensive inspection and testing of finished products, including electrical performance testing, appearance inspection, environmental adaptability testing, etc. Ensure that product performance and quality meet requirements, and trace and handle unqualified products.
- Establish a quality assurance system: Establish a complete quality assurance system, including quality planning, quality control, quality assurance, etc. Through continuous improvement and improvement of the effectiveness of the quality assurance system, we continuously improve the quality and reliability of our products.
To sum up, improving the quality and reliability of chip inductors requires starting from aspects such as material selection, manufacturing process, structural optimization and quality control.
Through reasonable material selection and manufacturing processes, optimizing product structure, and strengthening the construction of quality control and quality assurance systems, the quality and reliability of chip inductors can be effectively improved, providing a strong guarantee for the efficient and stable operation of electronic equipment.
Methods to improve the service life of chip inductors
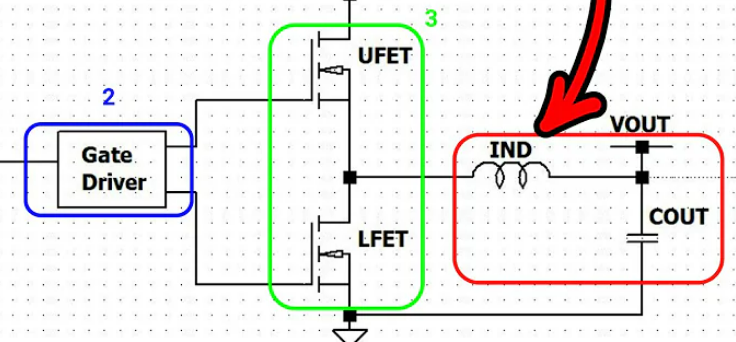
How to improve the service life of chip inductors? If you want to improve the service life of chip inductors, you can proceed from the following aspects:
Choose high-quality chip inductors: Choose inductor products produced by regular manufacturers to ensure their quality and reliability. Regular large manufacturers are more stringent in raw material procurement, production process control, quality inspection, etc., and can ensure the performance and quality of chip inductors. Chip inductors produced by regular manufacturers are more reliable in quality and have longer service life. When choosing chip inductors, you should give priority to brands and manufacturers with quality assurance.
Optimize the structure of the chip inductor: According to actual needs and application scenarios, optimize the coil, magnetic core and other structures of the chip inductor to improve its stability and reliability. For example, optimizing the winding method of the coil and increasing the cross-sectional area of the coil can improve the heating performance and reliability of the inductor.
Core material and structure have an important impact on the performance and service life of chip inductors. Choosing magnetic core materials with high magnetic permeability and low magnetic loss, as well as optimizing the structure and size of the magnetic core, can improve the stability and reliability of the chip inductor and extend its service life.
Select appropriate coil wire materials: The selection of coil wire materials has a crucial impact on the service life of the chip inductor.
Choosing high-temperature-resistant, low-impedance coil wire can improve the current-carrying capacity and reliability of the chip inductor, thereby extending its service life.
Choosing packaging materials with good temperature resistance, moisture resistance, corrosion resistance and other properties can improve the protection effect and service life of the chip inductor.
Choose high-temperature resistant, low-impedance coil wires: The selection of coil wires has a crucial impact on the service life of the chip inductor. Choosing high temperature resistant, low impedance coil wire can improve the current carrying capacity and reliability of the chip inductor.
Avoid overload use: When using chip inductors, overload use should be avoided to avoid problems such as coil overheating and core saturation, which will affect the service life of the chip inductor.
Pay attention to the working environment temperature: The working environment temperature of the chip inductor also affects its service life. The working environment temperature of the chip inductor should be reduced as much as possible and long-term high-temperature operation should be avoided to increase its service life.
Correct installation and use: When installing and using chip inductors, the correct direction and position should be followed to avoid the impact of mechanical stress, vibration and other factors on the chip inductor to ensure its service life.
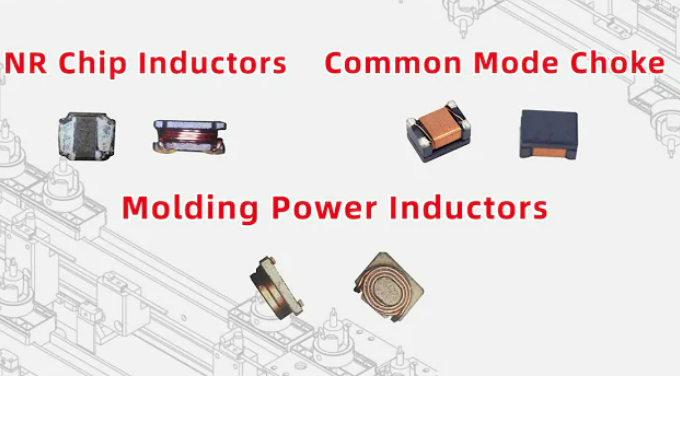
Regular maintenance and inspection: For chip inductors that have been used for a long time, regular maintenance and inspection should be carried out to detect and solve potential problems in time to extend their service life.
Improving the service life of chip inductors requires ensuring quality, optimizing structure, selecting appropriate coil wires, avoiding overload use, paying attention to the working environment temperature, correct installation and use, and regular maintenance and inspections.
To sum up, improving the service life of chip inductors requires selecting high-quality chip inductors, suitable coil wires, optimizing core materials and structures, avoiding overload use, paying attention to the working environment temperature, correct installation and use, and regular maintenance.
Start with inspection and selection of appropriate packaging materials. At the same time, in practical applications, you should also pay attention to comply with the usage specifications and precautions to ensure that the service life of the chip inductor is fully guaranteed.
How should the coil wires of chip inductors be selected and optimized
When selecting and optimizing coil wires for chip inductors, the following aspects need to be considered:
- DC resistance: The DC resistance of the coil wire will affect the heating performance and power consumption of the inductor. Choosing coil wire with lower DC resistance can improve the inductor’s heating performance and reliability.
- Current carrying capacity: The current carrying capacity of the coil wire is one of the key factors in selecting the wire. When selecting coil wires, wires with sufficient current carrying capacity should be selected based on the operating current and peak current requirements of the inductor.
- Mechanical strength: Coil wire needs to have a certain mechanical strength to withstand the mechanical stress during manufacturing and assembly. Choosing coil wire with higher mechanical strength can improve the stability and reliability of the inductor.
- High temperature resistance: The high temperature resistance of the coil wire is one of the key factors affecting the reliability of the inductor. Choosing coil wire materials with higher high temperature resistance can improve the service life and reliability of the inductor.
- Environmental protection requirements: In modern electronic products, environmental protection requirements are getting higher and higher. Choosing coil wires that meet environmental protection requirements, such as lead-free, low-smoke halogen-free and other environmentally friendly wires, can improve the environmental performance and market competitiveness of the inductor.
In order to optimize the selection of coil wire materials, the following aspects can be considered:
- Select appropriate coil wire specifications and models based on actual needs and application scenarios.
- On the premise of meeting performance requirements, give priority to coil wires with lower cost and environmental protection requirements.
- During the manufacturing process, pay attention to the quality control of the coil wire and the optimization of the processing technology to ensure the quality and reliability of the coil wire.
- During use, pay attention to the monitoring and adjustment of the working environment temperature and current carrying capacity of the coil wire to avoid the impact of overload and high temperature on the coil wire.
To sum up, selecting and optimizing coil wires for chip inductors requires comprehensive consideration of DC resistance, current carrying capacity, mechanical strength, high temperature resistance, environmental protection requirements and other factors.
At the same time, during the manufacturing and use processes, quality control and process optimization are strengthened to ensure the quality and reliability of coil wires, thereby improving the service life and stability of chip inductors.
So if the chip inductor has been damaged, is it still possible to repair it
Whether the chip inductor can be repaired after damage depends on the degree of damage and the specific cause. Here are some possible fixes:
- Replace the inductor: If the inductor is completely damaged or cannot be repaired, the best way is to replace it with a new inductor. Please note that if you know the model number of the inductor, you can buy it online and replace it yourself. If you are not sure about the model, it is best to consult a professional technician and ask them to replace it.
- Welding repair: If the coil of the inductor is disconnected or has poor contact, you can consider using welding to repair it. Please note that proper solder and soldering temperature should be used when soldering to avoid damage to other components.
- Winding the coil: If the coil of the inductor is damaged, consider re-winding the coil. Please note that proper wire diameter and number of turns should be used during winding to restore the electrical properties of the inductor.
- Secure the core: If the inductor’s core becomes loose or falls off, consider using appropriate glue or fixtures to re-fix the core in the correct position.
It should be noted that for some complex chip inductors, the repair process may require professional techniques and tools.
Therefore, before carrying out repairs, it is best to consult professional technicians or relevant experts to understand the feasibility of repairs and choose appropriate repair methods.
At the same time, when repairing and maintaining any electronic equipment, you must pay attention to safety to avoid damage to the equipment and people.
If my chip inductor is overloaded, how should I check and repair it
If the chip inductor is overloaded, you first need to check whether the appearance of the inductor is burnt, discolored, cracked, etc., and whether there is any abnormal sound or smell. These signs may indicate that the inductor is damaged.
If the visual inspection reveals no problems, you can use a multimeter to check the resistance value of the inductor. The resistance value of a normal inductor should be close to zero. If the resistance value is very large or infinite, it may indicate that the inductor has been damaged.
If it is determined that the inductor is damaged, the cause of the damage needs to be found and corresponding repair measures must be taken. Common repair methods include replacing inductors, welding repairs, winding coils, and fixing cores. The specific repair method needs to be determined based on the degree of damage and the cause of the damage.
When repairing chip inductors, you need to pay attention to safety issues. When replacing inductors or soldering, problems such as short circuits or overheating need to be avoided to avoid damage to the circuit board and other components. At the same time, appropriate tools and materials, such as suitable soldering stations, soldering tin, solder paste, etc., need to be used to ensure the quality and reliability of the repair.
In addition, in order to prevent overloading of chip inductors, some preventive measures can be taken, such as controlling the stability of the power supply voltage, avoiding overloading of the power supply line, and selecting appropriate inductors and components. These measures can effectively reduce the possibility of inductor overload and improve the stability and reliability of the circuit.
How should the withstand voltage and current values of chip inductors be selected and optimized
When selecting and optimizing the withstand voltage and current values of chip inductors, the following aspects need to be considered:
- Circuit requirements: Determine the required withstand voltage and current values based on the operating voltage and current of the circuit. If the working voltage of the circuit is high, you need to choose an inductor with a higher withstand voltage value; if the working current of the circuit is large, you need to choose an inductor with a larger current value.
- Magnetic core material: Parameters such as magnetic permeability and saturation flux density of the magnetic core material will affect the performance of the inductor. Choosing a core material with high magnetic permeability and saturation flux density can improve the withstand voltage and current values of the inductor.
- Coil wire: Parameters such as the cross-sectional area and resistance value of the coil wire will also affect the performance of the inductor. Choosing a coil wire with a larger cross-sectional area and smaller resistance value can increase the current value of the inductor.
- Package size: Package size will affect the heat dissipation performance and mechanical strength of the inductor. When selecting the package size, heat dissipation needs and mechanical strength requirements need to be considered to ensure the performance and reliability of the inductor.
- Working environment temperature: The working environment temperature of the inductor will affect its performance and reliability. When selecting an inductor, you need to consider the influence of the working environment temperature and select an inductor with corresponding temperature resistance.
In order to optimize the withstand voltage value and current value of the chip inductor, the following aspects can be considered:
- Optimize the structure and size of the magnetic core: By optimizing the structure and size of the magnetic core, the withstand voltage and current values of the inductor can be further improved. For example, increasing the cross-sectional area of the magnetic core and reducing the number of turns of the coil can increase the current value.
- Optimize the coil design: Optimizing the coil design can improve the performance and reliability of the inductor. For example, adopting appropriate winding methods and number of turns, selecting appropriate coil wire materials and other measures can improve the current value and voltage resistance value of the inductor.
- Strengthen the heat dissipation design: Strengthening the heat dissipation design can improve the heat dissipation performance and stability of the inductor. For example, measures such as adding heat sinks and improving heat dissipation channels can improve the withstand voltage and current values of the inductor.
- Use high-quality raw materials: Using high-quality raw materials can improve the performance and reliability of the inductor. For example, choosing core materials with high magnetic permeability and saturation magnetic flux density, selecting coil wires with low resistance values, and other measures can improve the withstand voltage and current values of the inductor.
To sum up, selecting and optimizing the voltage and current values of chip inductors requires comprehensive consideration of circuit requirements, core materials, coil wires, package size, working environment temperature, etc.
At the same time, during the manufacturing and use processes, quality control and process optimization are strengthened to ensure the quality and reliability of chip inductors.
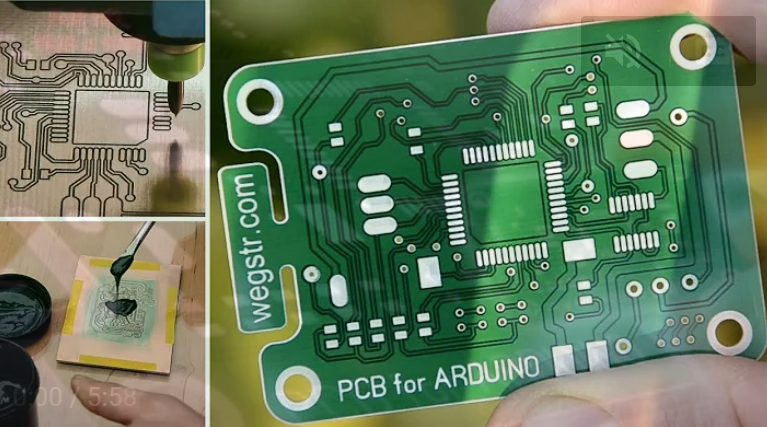
What are the main factors of the temperature resistance of the patch
The temperature resistance of the patch inductor mainly depends on the following factors:
- The quality of raw materials: High -quality raw materials have better stability and reliability, and can effectively extend the life of the inductance. For example, a magnetic core material with high magnetic guidance, low magnetic damage, and coil wires with high temperature resistance and low impedance.
- Structural design: By optimizing the structural design of the inductance, the heat loss of the inductance can effectively reduce the heat loss of the inductance in high temperature, thereby improving the temperature resistance. For example, measures such as optimizing coil winding and increasing the cross -area of the coil can improve the thermal performance and reliability of the inductance.
- Heating design: In order to prevent inductance from overheating in high temperature environments, the heat dissipation design of inductance needs to be strengthened. For example, increased heat dissipation pieces and selection of materials with good thermal conductivity can improve the heat dissipation performance and temperature resistance of inductance.
- Production process: In the process of inductance, the production process must be strictly controlled to ensure the quality of the inductance, and the temperature resistance of temperature resistance is reduced due to the problem of production technology. For example, strictly control the winding process of the coil and the assembly process of magnetic cores.
In summary, the temperature resistance of improving the inductance of the patch needs to be started from choosing high -quality raw materials, optimizing structural design, strengthening heat dissipation design, and strict control of production technology.
At the same time, in practical applications, we should also pay attention to compliance with the use specifications and precautions to ensure that the temperature resistance of the patch is fully guaranteed.