
SMT anti-static splicing tape equipment process flow
SMT (Surface Mount Technology) automatic tape splicing equipment is a key automation technology in electronic manufacturing.
It is mainly used for sorting, counting and detecting SMT disc tapes. The application of this technology makes the electronic manufacturing process more efficient and accurate, and promotes the progress of the entire electronics industry.
Guangdong Guoyu Technology SMT anti-static splicing tape equipment part
One of the primary functions of this equipment is the sorting of SMT disc tapes. In the traditional electronics assembly process, manual sorting of material strips is relatively inefficient and contains errors. However, the automatic splicing strip equipment can quickly and accurately identify and sort disk-shaped materials through advanced vision systems and robotic arm technology.
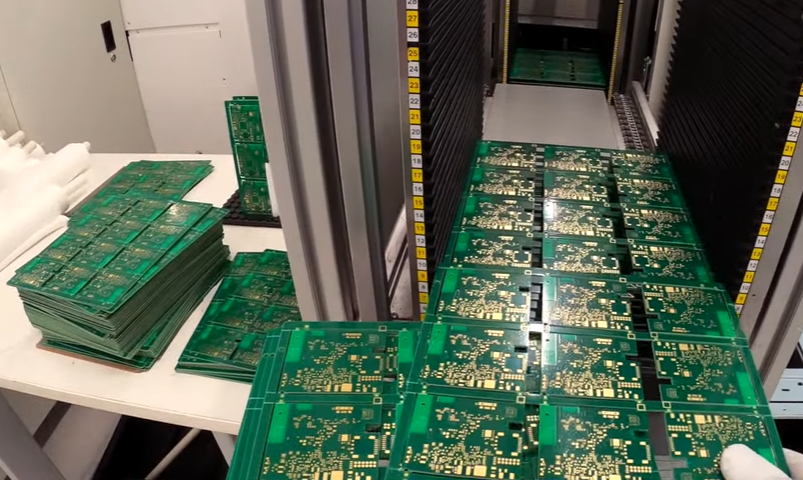
Various components on the belt. This not only improves production efficiency, but also reduces the possibility of human error and provides a reliable foundation for subsequent production links.
Secondly, this equipment plays a key role in counting SMT disc tapes. Through precise counting functions, automatic tape splicing equipment can quickly and accurately confirm the number of components in each tape. This helps ensure that insufficient or redundant components do not occur during assembly, thereby improving product quality and reliability.
SMT automatic splicing tape
In addition, the SMT anti-static splicing tape equipment also has the function of detecting components. Through advanced sensors and detection technology, the equipment can detect key information such as the quality, orientation and location of components. This helps to detect possible defects or anomalies in time, ensures that only components that meet standards are used for assembly, and improves the stability and controllability of the entire production line.
The advantage of this automation technology lies not only in improving production efficiency and product quality, but also in its saving of human resources. Compared with traditional manual operation, SMT anti-static splicing tape equipment is not only faster and more accurate, but also can run continuously, reducing production risks caused by human factors.
The widespread application of SMT anti-static splicing tape equipment has enabled the electronics manufacturing industry to make significant progress in improving production efficiency, reducing costs, and improving product quality.
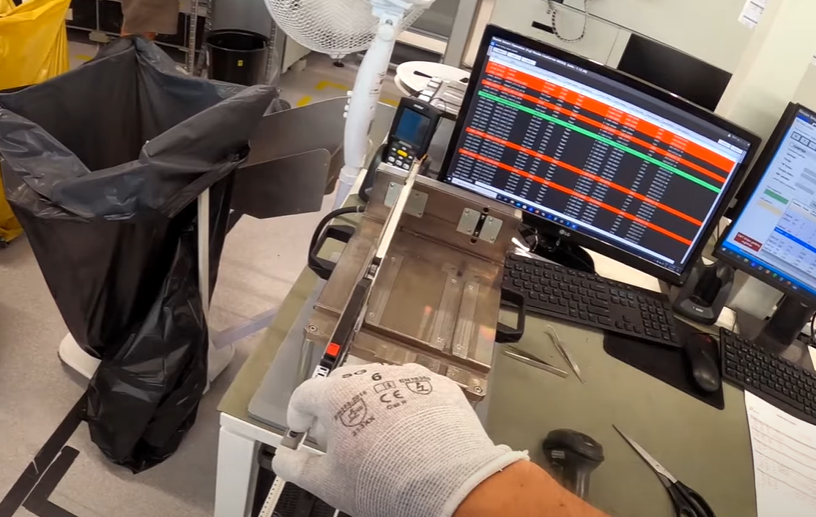
This advanced technology plays an irreplaceable role in meeting the needs of the modern electronics industry for efficient, precise and reliable production, laying a solid foundation for the future development of the electronics manufacturing industry.
Overview of the process flow of SMT anti-static splicing tape equipment
In Surface Mount Technology (SMT), anti-static splicing tape equipment is an important auxiliary equipment, mainly used to prevent static electricity from damaging electronic components.
The process flow mainly includes the following steps: splicing tape supply, splicing tape positioning, electronic component placement, welding, inspection and testing.
- Supply of splicing tape: The splicing tape is pulled out from the reel and passes through the guide wheel and tension wheel to maintain a certain tension to ensure its stable position during the production process.
- Splice tape positioning: Before placing electronic components on the circuit board, the splice tape is accurately placed at a specific location on the circuit board to secure the electronic components.
- Electronic component placement: Use an automatic or semi-automatic component placement machine to place electronic components on the splicing tape.
- Welding: Use welding techniques such as hot melt welding or ultrasonic welding to connect electronic components to circuit boards.
- Inspection and testing: Conduct quality inspection and performance testing on the soldered circuit board to ensure that it meets the preset quality standards.
Each step is critical to the quality and reliability of the final product, so the operating parameters and process conditions of each link need to be strictly controlled.
Detailed introduction to the process flow of anti-static splicing tape equipment
- Supply of splicing tape: The splicing tape is pulled out from the reel, passes through the guide wheel and tension wheel, and enters the production area. The function of the guide wheel and tension wheel is to control the speed and tension of the splicing belt to ensure its stability during the production process. In addition, in order to prevent static electricity from damaging electronic components, an anti-static coating is usually added to the splicing tape.
- Splice tape positioning: Before electronic components are placed on the circuit board, the splice tape is accurately placed at a specific location on the circuit board. This step is usually completed by a positioning system, which can adjust the position of the splicing strip according to the reference point on the circuit board to ensure the accuracy of component placement. At the same time, in order to ensure production efficiency, the positioning system should also have the ability to adjust the position quickly and accurately.
- Electronic component placement: Use an automatic or semi-automatic component placement machine to place electronic components on the splicing tape. The component placement machine can accurately place electronic components on the splicing tape according to preset data and programs. In order to ensure the accuracy and stability of component placement, component placement machines need to be calibrated and maintained regularly.
- Welding: Use welding techniques such as hot melt welding or ultrasonic welding to connect electronic components to circuit boards. During the welding process, attention needs to be paid to the control of parameters such as temperature, time and pressure to ensure welding quality. At the same time, in order to prevent the impact of static electricity on welding, corresponding anti-static measures need to be taken, such as grounding and using an anti-static workbench.
- Inspection and testing: Conduct quality inspection and performance testing on the soldered circuit board to ensure that it meets the preset quality standards. Various inspection tools and technologies are required during the inspection and testing process, such as visual inspection, electrical performance inspection, etc. At the same time, defective products also need to be traced and processed to reduce the defective rate.
In general, the SMT anti-static splicing tape equipment process requires strict control of the operating parameters and process conditions of each link to ensure the quality and reliability of the final product.
In actual production, adjustments and optimizations need to be made according to specific circumstances to improve production efficiency and reduce costs.