The manufacturing process of transistor manufacturers is a highly complex and precise technology involving multiple steps, including crystal growth, wafer preparation, doping, etching, electrode fabrication and packaging.
Each step requires strict quality control and precise operations to ensure the performance and consistency of the final product. Still, transistor manufacturing faces challenges such as high material costs, difficulties with precise doping, packaging and testing challenges, and pressure to continually upgrade technology. In order to overcome these challenges, transistor manufacturers continue to strive to improve the level and technological content of manufacturing processes to provide high-quality, high-performance transistor products.
What do transistor manufacturers do?
Transistor manufacturers are manufacturers that specialize in producing transistors. Their main job is to manufacture and produce transistors to meet the needs of different electronic devices.
Transistor is a semiconductor device with high sensitivity, low noise, high reliability, stability and other characteristics. It is widely used in various electronic devices, such as televisions, computers, mobile phones, etc. With the continuous development of science and technology, there are more and more types and specifications of transistors, and their application fields are becoming more and more extensive.
The work of transistor manufacturers includes manufacturing and R&D of transistors, as well as providing technical support and after-sales services. They use advanced production processes and equipment to precisely control the material, size, shape, doping and other parameters of the transistor to ensure that its electrical characteristics and performance meet the requirements.
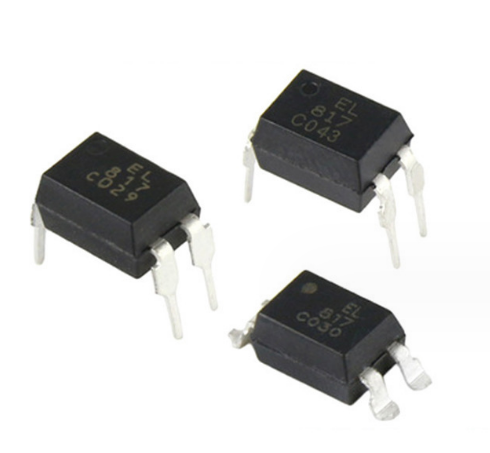
In addition to manufacturing transistors, some transistor manufacturers also provide customization services, designing and producing specific transistors based on customer needs and specifications.
Transistor manufacturers are manufacturers that specialize in the production of transistors. They are committed to providing high-quality, high-performance transistor products to meet the needs of different applications.
Why do transistor manufacturers make transistors?
Transistor manufacturers make transistors for the following reasons:
Achieve miniaturization and efficiency
A transistor is a semiconductor device whose size and shape affect its electrical properties. By precisely controlling the size and shape of transistors, more efficient and smaller electronic devices can be achieved.
Improve equipment reliability and stability
Transistors have high reliability and stability, which allows them to function well in a variety of environments. Transistors are very important components for some devices that require long-term operation or high-precision control.
Achieve high sensitivity and low noise performance
The transistor has high sensitivity and low noise performance, can operate normally in a weak signal environment, and can also achieve high-precision signal processing.
Meet different application needs
There are many types and specifications of transistors to meet the needs of different applications. For example, some special types of transistors can be used to operate in high power, high frequency, or high temperature environments.
Achieve mass production
With the development of semiconductor technology, the production of transistors has achieved large-scale production, which makes their prices relatively low and also laid the foundation for the popularization of electronic devices.
The transistor is an important semiconductor device with many advantages and uses. Therefore, transistor manufacturers are committed to manufacturing and developing transistors to meet the needs of different applications.
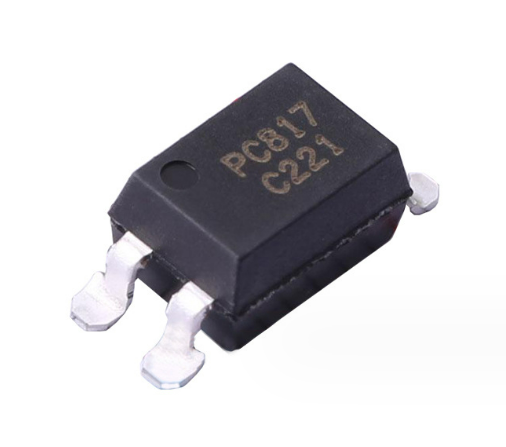
What is the manufacturing process of transistor manufacturers?
The manufacturing process of transistor manufacturers includes multiple steps. The following is a detailed description:
crystal growth
This is the first step in making a transistor, whose core component is a semiconductor material, usually silicon. High-purity silicon material is heated and melted, and then the conductive properties of the crystal are controlled by introducing impurity atoms to obtain single-crystal silicon rods with specific properties. This process can use a variety of methods, including the Czochralski method, zone melting method, floating zone method, etc.
Wafer preparation
Wafers are the basis for transistor production, usually using monocrystalline silicon or polycrystalline silicon materials. The silicon material is subjected to multiple high-temperature treatments to turn it into pure polysilicon rods, which are then sawed into thin slices to form 8-inch diameter discs, known as wafers.
Doping
The purpose of doping is to change certain properties of the material by adding other elements without changing the basic chemical structure of the material. During the fabrication of transistors, doping helps control their conductive properties.
butterfly etching
Butterfly etching is a common etching technology during transistor manufacturing. With this technique, specific shapes and sizes can be carved into silicon wafers to achieve precise control of electrical current.
Electrode production
One of the key parts of a transistor is the electrode, which is used to guide the flow of electricity. During the manufacturing process, electrodes need to be accurately formed on the silicon wafer and ensure good contact between the electrodes and the semiconductor material.
transistor package
Finally, transistors need to be packaged to protect their internal semiconductor materials and electrodes. Packaging protects the transistor from external environmental influences and also allows the transistor to be connected to external circuitry.
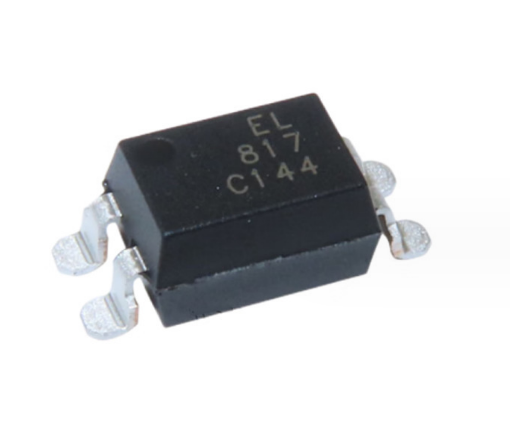
The above are the main steps of the manufacturing process of transistor manufacturers and are also the key steps of the transistor manufacturing process. It should be noted that the equipment and materials used in different process steps may be different, and the specific manufacturing process will also vary depending on the manufacturer and product type.
Challenges and difficulties in the manufacturing process of transistor manufacturers
The challenges and difficulties faced by transistor manufacturers in the manufacturing process mainly include the following aspects:
Process complexity
The manufacturing process of transistors is very complex and requires precise control of every production link. For example, when manufacturing transistors, it is necessary to precisely control the purity, thickness, doping and other parameters of the material to ensure that its electrical characteristics and performance meet the requirements. In addition, high-precision manufacturing equipment and technology are also required to ensure that the manufactured transistors have high precision, high consistency, and high stability.
High cost of materials
Transistor manufacturing requires the use of a variety of high-purity, high-precision materials, such as monocrystalline silicon, silicon oxide, polycrystalline silicon, gallium arsenic, etc. These materials are more expensive, and some materials are more difficult to produce and process, resulting in higher manufacturing costs for transistors.
The challenge of precision doping
Doping is one of the important links in transistor manufacturing, which directly affects the electrical characteristics and performance of the transistor. However, controlling the accuracy and consistency of doping is difficult and requires the use of advanced equipment and manufacturing techniques.
Packaging and testing challenges
After the transistor is manufactured, it needs to be packaged and tested. In this link, it is necessary to ensure the safety and stability of the transistor, and at the same time ensure that its electrical characteristics and performance meet the requirements. This requires the use of high-precision test equipment and testing techniques to ensure that the quality and performance of each transistor is up to standard.
The pressure of continuous technological upgrading
With the continuous development of technology, there are more and more types and specifications of transistors, and the requirements for manufacturing processes are getting higher and higher. In order to remain competitive, transistor manufacturers need to continuously upgrade technology and equipment to meet changing market demands.
The transistor manufacturing process faces challenges such as complexity, high cost, precise doping, packaging testing and constant upgrade pressure. In order to overcome these challenges, transistor manufacturers need to continuously improve the level and technical content of their manufacturing processes to provide high-quality, high-performance transistor products.
How do transistor manufacturers overcome the challenge of high material costs?
Transistor manufacturers can take several approaches to overcome the challenge of high material costs:
Find alternative materials
Look for lower-priced, better-quality alternative materials to reduce the cost of manufacturing transistors. For example, some transistor manufacturers have begun to use compound semiconductor materials, such as gallium arsenide (GaAs), to replace traditional silicon materials.
Improve material utilization
By improving the manufacturing process and optimizing product design, the utilization rate of transistor materials is increased, waste is reduced and costs are reduced.
Achieve large-scale production
Economic benefits can be achieved by expanding production scale, increasing output and reducing unit costs.
Strengthen supply chain management
Optimize supply chain management, select reliable suppliers, and establish long-term and stable cooperative relationships to reduce material costs and procurement risks.
Carry out technology research and development and innovation
Through technological research and development and innovation, we continuously upgrade manufacturing processes and equipment to improve production efficiency and product quality, thereby reducing manufacturing costs.
Optimize product design and functionality
On the premise of meeting product performance and functional requirements, optimize product design as much as possible to reduce unnecessary material consumption and manufacturing costs.
Strengthen communication and cooperation with customers
Establish a good communication and cooperation mechanism with customers, understand market demands and product applications, and jointly promote the development and application of transistor manufacturing technology.
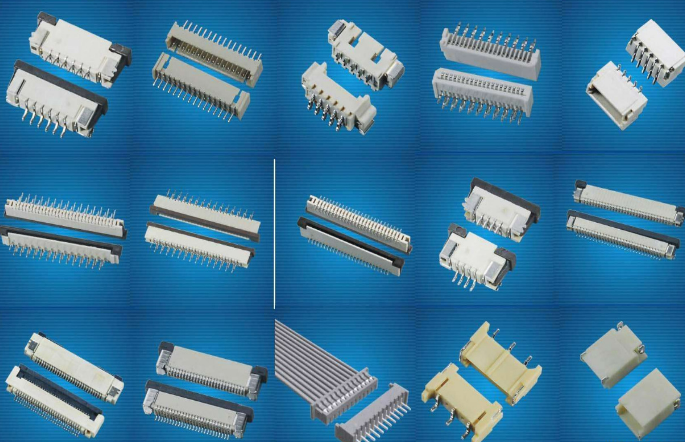
Transistor manufacturers need to take a variety of measures to overcome the challenge of high material costs, including finding alternative materials, improving material utilization, achieving large-scale production, strengthening supply chain management, carrying out technology research and development and innovation, optimizing product design and functions, and strengthening communication with Customer communication and cooperation, etc. These measures help reduce the manufacturing cost of transistors and improve product competitiveness and market share.
Precautions for manufacturing transistor manufacturers
Transistor manufacturers need to pay attention to the following matters during the manufacturing process:
material selection
Selecting the appropriate semiconductor material, such as silicon (Si) or compound semiconductor material, has an important impact on the performance of the transistor.
cleanse and purify
Before manufacturing, the processing environment needs to be cleaned and purified to avoid dust, impurities, etc. from affecting the quality of the transistors.
Control size and shape
The size and shape of transistors are precisely controlled to ensure their electrical characteristics and performance meet requirements.
Doping and diffusion
The conductive properties of semiconductor materials are changed through doping and diffusion technologies to form P-type and N-type regions in electronic devices, thereby realizing the working principle of transistors.
Operating frequency and switching status
The transistor must work in a switching state, and the operating frequency must be less than the cut-off frequency of the transistor to ensure its normal operation and stability.
Withstand voltage and current requirements
The withstand voltage is 2 to 3 times greater than the maximum operating voltage, and the current value is greater than 2 times the operating current to ensure the safety and reliability of the transistor during use.
Packaging and testing
After the transistor is manufactured, it needs to be packaged and tested. In this link, it is necessary to ensure the safety and stability of the transistor, and at the same time ensure that its electrical characteristics and performance meet the requirements.
Technology upgrading and research and development
With the continuous development of science and technology and changes in market demand, transistor manufacturers need to continuously upgrade technology and equipment, conduct research and development and innovation to meet the changing market demand and improve the competitiveness of their products.
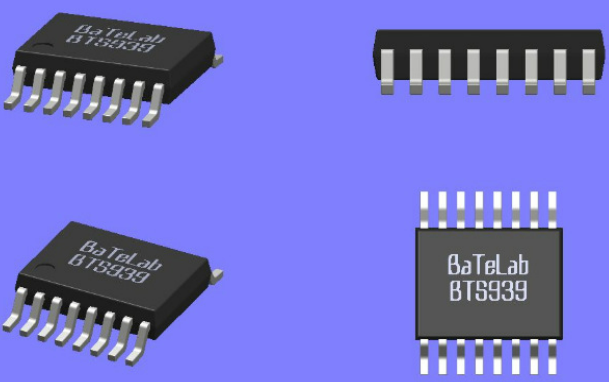
There are many aspects that need to be paid attention to during the transistor manufacturing process to ensure that the manufactured transistors have high quality, high performance and reliability to meet the needs of different applications.
What chemicals do transistor manufacturers use?
The chemical materials used by transistor manufacturers mainly include semiconductor materials and auxiliary materials.
Semiconductor materials are the core raw materials for making transistors, and commonly used materials include silicon (Si) and germanium (Ge). These materials have special conductive properties and can realize the production of PN junctions and switches of transistors by controlling parameters such as impurity content and material purity.
In addition to semiconductor materials, transistor manufacturers also use some auxiliary materials, which are used to make transistor electrodes, insulating layers, and heat sinks. Common auxiliary materials include metal materials, insulation materials, thermal conductive materials, etc.
Metal materials are mainly used to make the electrodes of transistors, such as aluminum (Al), copper (Cu), gold (Au), and silver (Ag). These metal materials have excellent electrical conductivity, can provide good electrical contact, and can also be used as part of the heat sink.
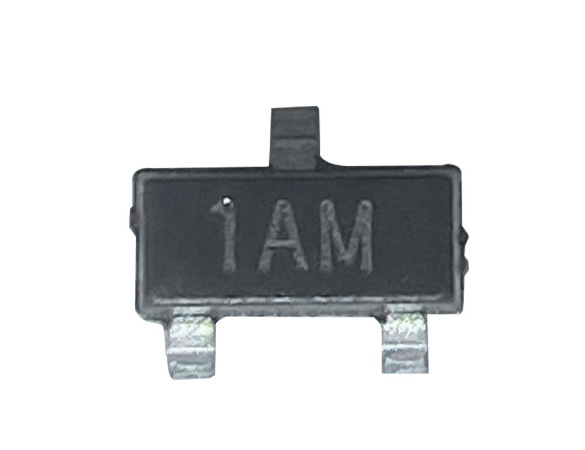
Insulating materials are mainly used to make the insulating layer of transistors, such as silicon dioxide (SiO2), silicon nitride (Si3N4), etc. These materials have high insulating properties and can effectively isolate the electrical contact between the transistor and other electronic components, ensuring the stability and reliability of the transistor.
Thermal conductive materials are mainly used to make heat sinks for transistors, such as copper substrates, aluminum substrates, etc. These materials have excellent thermal conductivity and can quickly dissipate the heat generated by the transistor to ensure the stability and reliability of the transistor.
It should be noted that different transistor materials have different chemical and physical properties. Therefore, transistor manufacturers need to consider the characteristics and application range of different materials when selecting materials to ensure that the manufactured transistors have high quality, high performance and reliability. Features. At the same time, since these chemical materials may have an impact on the environment and human body, corresponding safety and environmental protection measures need to be taken during use.
Do transistor manufacturers offer custom transistors?
Yes, many transistor manufacturers offer custom transistor services. These manufacturers can design and produce specific transistors based on customer needs and specifications.
In terms of custom transistors, manufacturers usually communicate and cooperate closely with customers to understand their needs and requirements, and then design and produce according to their requirements. Some manufacturers also provide comprehensive technical support and after-sales service to ensure that customers receive transistors that meet their specific needs.
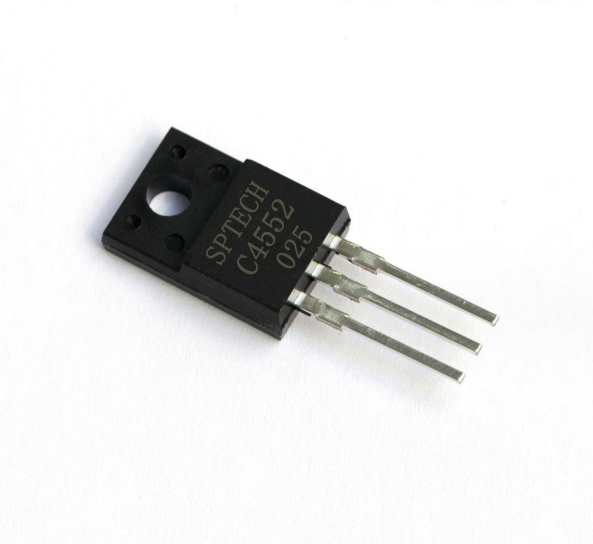
It should be noted that customizing transistors usually requires a certain production cycle and cost, so customers need to plan their needs in advance and fully communicate and negotiate with manufacturers to ensure that they can obtain transistors that meet their needs on time.