Introduction
In modern electronics, current sources and bias transistors play a vital role. These basic components are widely used in various electronic devices such as amplifiers, oscillators, logic gates, etc.
However, there are still many unsolved mysteries in academia and industry regarding the special structure of biased transistors in current sources. This article will detail the special structures of biased transistors and how these structures affect the performance of current sources.
Basic structure and working principle of biased transistor
First, we need to understand the basic structure of a biased transistor and how it works. A triode is an electronic device made of a semiconductor material (usually silicon or germanium) and has three electrodes: base (B), collector (C) and emitter (E). In a current source, the main function of a bias transistor is to provide and regulate a constant current. This current can be used as the operating current for amplifiers, oscillators, or other electronic devices.
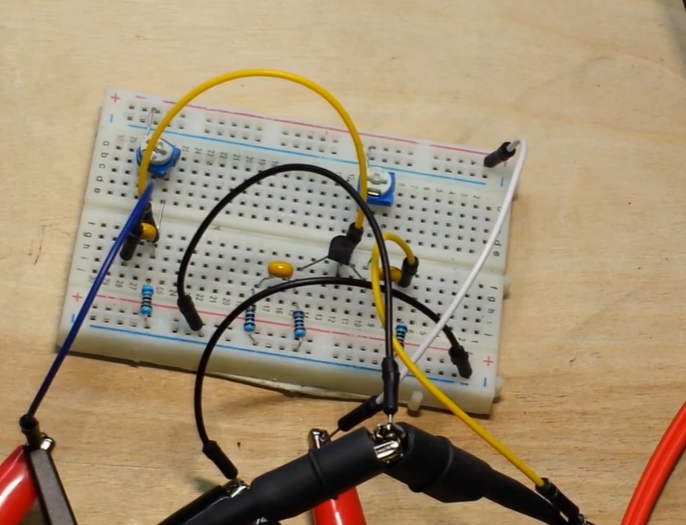
Effect of special structure on current source performance
Special structure refers to additional designs or modifications introduced during the manufacturing process of a triode to improve its performance or meet specific application needs. These special structures may include: base region doping gradient design, emitter shape adjustment, collector structure design, etc.
- Base region doping gradient design: The base region is the part of the triode that connects the base and collector. By changing the doping concentration of the base region, the size and distribution of the collector current can be affected, further affecting the output stability of the current source.
- Emitter shape adjustment: The emitter is the part of the triode that connects the base and collector. Changing the shape of the emitter, such as increasing the emitter area or introducing a groove structure, can optimize the current distribution and improve the efficiency of the current source.
- Collector structure design: The collector is the electrode that collects electrons in the triode. By changing the structure of the collector, such as increasing the length of the collector or changing the width of the collector, the cutoff frequency and maximum oscillation frequency of the triode can be adjusted, thereby affecting the bandwidth and stability of the current source.
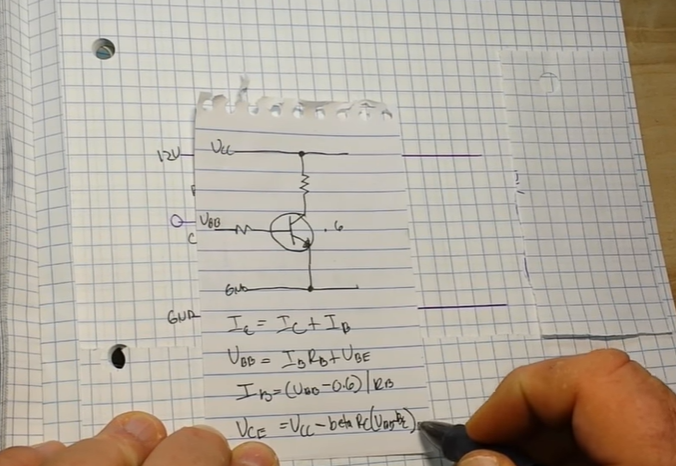
Practical application case analysis
To gain a deeper understanding of how these special structures affect the performance of current sources, we will analyze some real-world application cases. For example, in audio amplifiers, using triodes with special emitter designs can reduce harmonic distortion and improve sound quality; in high-speed digital circuits, using triodes with optimized collector structures can reduce signal delay and increase the operating frequency of the circuit.
Future research directions and prospects
With the continuous development of science and technology, the research on the special structure of the biased transistor in the current source is also in-depth. Future research directions may include: exploring the application of new materials in biased triodes, developing smart triodes with adaptive functions, and studying the collaborative working mechanism of triodes and other electronic components. Through these studies, we are expected to further improve the performance of current sources and promote the development of electronic technology.
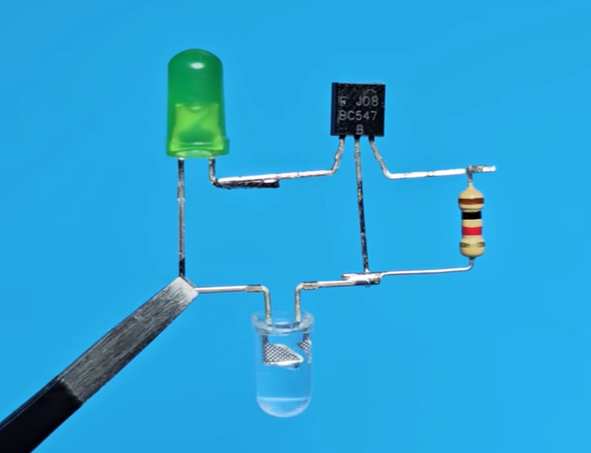
In conclusion
This article conducts an in-depth discussion of the special structure of the biased transistor in the current source and analyzes the impact of the special structure on the performance of the current source.
By understanding these effects, we can better design and optimize current sources in electronic devices, improving their performance and stability.
At the same time, we also see broad prospects for future research, which will have a profound impact on the development of electronic technology.
Frequently Asked Questions
A biased transistor is an electronic device made of a semiconductor material (usually silicon or germanium) with three electrodes: base (B), collector (C), and emitter (E). In current sources, the main function of the bias transistor is to provide and regulate a constant current, which can be used as the operating current of amplifiers, oscillators or other electronic devices.
Special structure refers to additional designs or modifications introduced during the manufacturing process of a triode to improve its performance or meet specific application needs. These special structures may include base region doping gradient design, emitter shape adjustment, collector structure design, etc. These special structures can affect the performance of the current source, such as output stability, efficiency, bandwidth and stability.
The doping gradient design of the base region refers to affecting the size and distribution of the collector current by changing the doping concentration of the base region. By optimizing the doping concentration of the base region, the output stability of the current source can be further optimized. This design enables the current source to maintain a stable output under different operating conditions, thereby improving its performance.
Emitter shape adjustment refers to changing the shape of the emitter, such as increasing the emitter area or introducing a groove structure. By optimizing the shape of the emitter, the efficiency of the current source can be further optimized. This design can improve the uniformity of current distribution and reduce energy loss, thereby improving the efficiency of the current source.
Collector structure design refers to changing the structure of the collector, such as increasing the length of the collector or changing the width of the collector. This design can adjust the cutoff frequency and maximum oscillation frequency of the triode, thereby affecting the bandwidth and stability of the current source. By optimizing the structural design of the collector, the bandwidth and stability of the current source can be improved, allowing it to maintain stable output under different operating conditions.
In practical applications, selecting a suitable biased transistor requires considering its special structure, performance parameters, and application requirements. Based on the circuit requirements and comparison of performance parameters, a transistor with an appropriate special structure can be selected to optimize the performance of the current source. In addition, other parameters of the transistor need to be considered, such as breakdown voltage, collector current and noise.