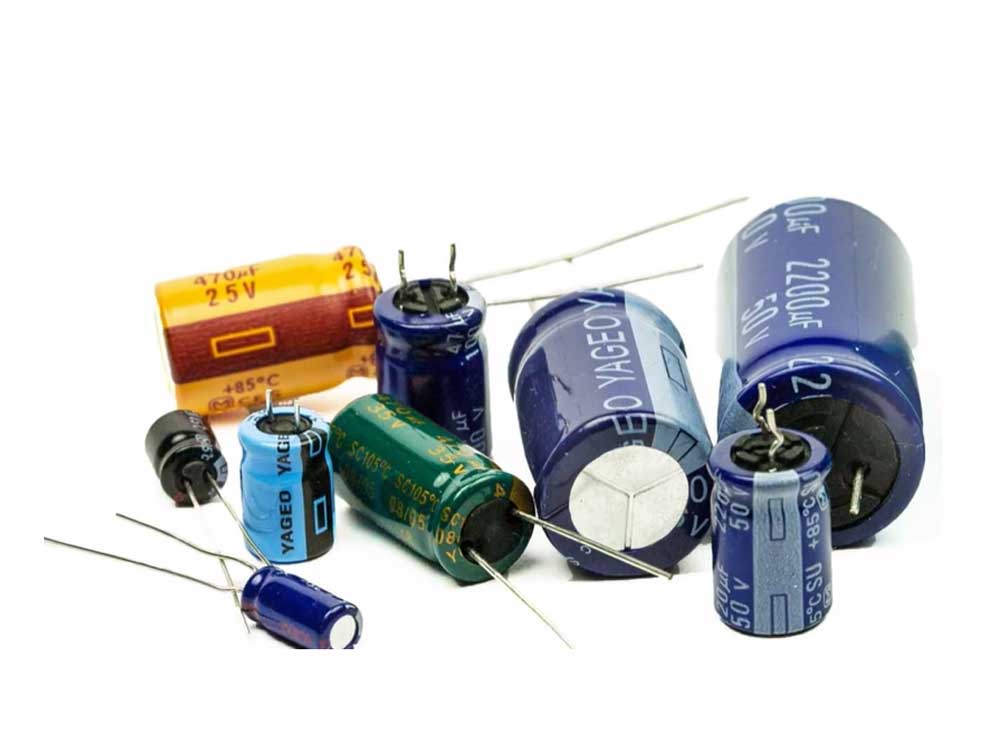
Electrolytic capacitor design and manufacturing specifications
Electrolytic capacitor design and manufacturing specifications are key factors in ensuring product quality and reliability.
They involve dielectric material selection, plate design, sealing and housing requirements, pin and connection regulations, and temperature characteristics. Strict compliance with these specifications is necessary to manufacture high-performance electrolytic capacitors.
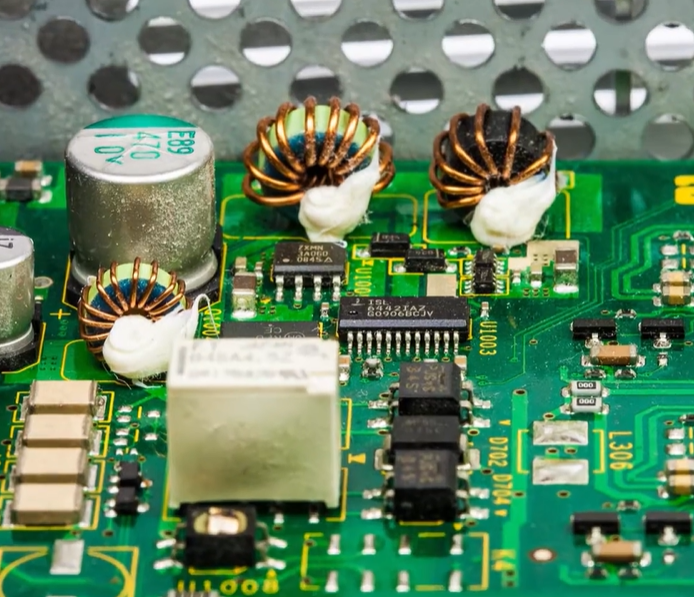
The design and manufacturing specifications of electrolytic capacitors is a complex and specialized field that encompasses knowledge from multiple disciplines, including electrical engineering, chemistry, physics, and materials science.
The following is a detailed introduction to electrolytic capacitor design and manufacturing specifications.
Design specifications
Dielectric material
Choosing the appropriate dielectric material is one of the key factors in the design of electrolytic capacitors. Commonly used dielectric materials include aluminum, tantalum, niobium, etc. According to different application requirements, select dielectric materials with appropriate dielectric constant, breakdown voltage and physical properties.
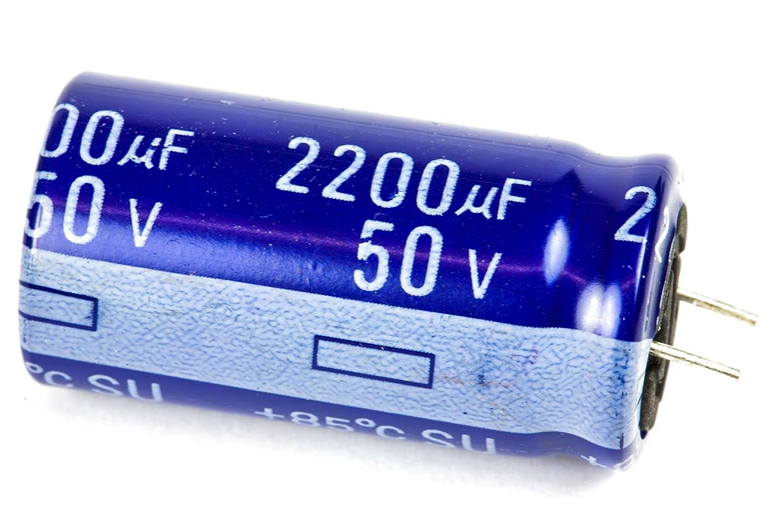
Plate design
The plate is the core part of the electrolytic capacitor and consists of a positive plate and a negative plate. The positive plate usually uses metal foil, while the negative plate uses a corresponding dielectric material. The design of the plate should consider current capacity, voltage resistance, mechanical strength and stability requirements.
Sealing and housing
The sealing and housing design of electrolytic capacitors should have sufficient mechanical strength and airtightness to protect the internal capacitor components from the external environment. In addition, the shape and size of the enclosure should comply with relevant standards and specifications to ensure its correct installation and connection in the circuit.
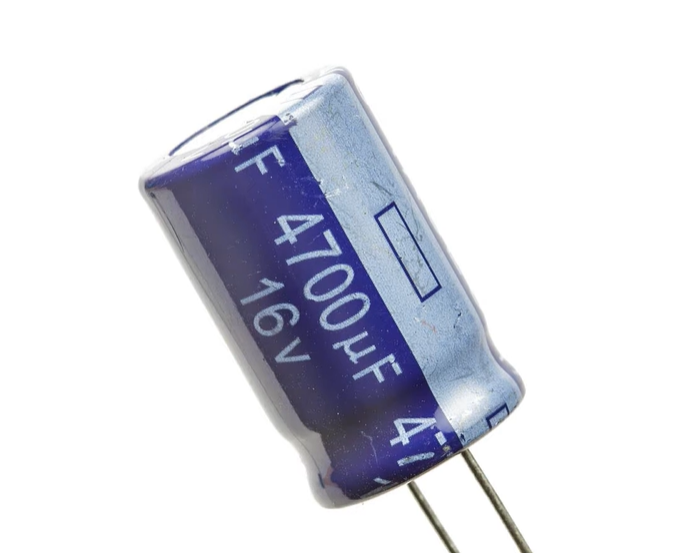
Pins and connections
The pins and connections of the electrolytic capacitor should be designed to ensure reliable connection to the circuit board. The pin material selection should be compatible with the circuit board material to avoid corrosion and oxidation. At the same time, the length and diameter of the pins should meet the corresponding mechanical strength and electrical performance requirements.
Temperature characteristics
The temperature characteristics of electrolytic capacitors should also be considered during the design and manufacturing process. Temperature has a great impact on the performance and service life of electrolytic capacitors, so appropriate materials and processes should be selected to maintain stable performance under various temperature conditions.
Manufacturing Specifications
Preparation process
Before manufacturing electrolytic capacitors, a series of preparations are required. It includes cleaning, cutting, coating and other process steps to ensure that the surface of the capacitor components is clean and smooth, laying a good foundation for the subsequent manufacturing process.
Winding process
The winding process of electrolytic capacitors is the process of winding the positive plate, dielectric material and negative plate together in a certain order to form the capacitor element. The key to the winding process is to control the tension, speed and direction of the winding to ensure the density and consistency of the components.
Pin welding
Pin welding is the process of soldering the pins of an electrolytic capacitor to the corresponding terminals. Welding temperature, time and pressure should be controlled during welding to ensure welding quality and avoid false welding, false welding and other phenomena.
Assembly process
The assembly process of electrolytic capacitors is the process of installing the manufactured capacitor components into the corresponding shell and performing sealing treatment.
During the assembly process, care should be taken to protect the components from damage while ensuring the airtightness and aesthetics of the housing.
Aging and testing
Aging and testing are indispensable links in the manufacturing process and are used to check and evaluate the performance and stability of electrolytic capacitors.
The aging process usually includes high-temperature aging, low-temperature aging, humidity aging and other links to simulate the actual working conditions of the capacitor.
Testing includes electrical performance testing, mechanical performance testing and environmental adaptability testing to ensure that the product meets relevant standards and specifications.
Packaging and transportation
Packaging and transportation of electrolytic capacitors are also important aspects of manufacturing specifications. Packaging materials should be moisture-proof, shock-proof, and dust-proof to ensure that the product is not damaged during transportation. At the same time, the markings on the packaging should be clear and accurate to facilitate product traceability and management.
In general, the design and manufacturing specification of electrolytic capacitors is a complex and rigorous process that requires comprehensive consideration of multiple factors.
Quality and process parameters must be strictly controlled in every aspect from design to manufacturing to ensure that the performance and reliability of the final product meet expected standards and requirements.
At the same time, it is also very important to continuously improve and optimize the design and manufacturing process to further enhance the competitiveness of products.
Frequently Asked Questions
Commonly used dielectric materials for electrolytic capacitors include aluminum, tantalum, niobium, etc. Depending on the application requirements, dielectric materials with appropriate dielectric constant, breakdown voltage, and physical properties can be selected.
The plate design of electrolytic capacitors should consider current capacity, withstand voltage, mechanical strength and stability requirements. The positive plate usually uses metal foil, while the negative plate uses a corresponding dielectric material.
The seal and housing design of electrolytic capacitors should have sufficient mechanical strength and airtightness to protect the internal capacitor components from the external environment. The shape and size of the enclosure should comply with relevant standards and specifications to ensure its correct installation and connection in the circuit.
The pins and connections of the electrolytic capacitor should be designed to ensure a reliable connection to the circuit board. The pin material selection should be compatible with the circuit board material to avoid corrosion and oxidation. At the same time, the length and diameter of the pins should meet the corresponding mechanical strength and electrical performance requirements.
The temperature characteristics of electrolytic capacitors should be considered during the design and manufacturing process. Temperature has a great impact on the performance and service life of electrolytic capacitors, so appropriate materials and processes should be selected to maintain stable performance under various temperature conditions.
The winding process of electrolytic capacitors is the process of winding the positive plate, dielectric material and negative plate together in a certain order to form the capacitor element. The key to the winding process is to control the tension, speed and direction of the winding to ensure the density and consistency of the components.
Pin soldering of electrolytic capacitors is the process of soldering the pins to the corresponding terminals. Welding temperature, time and pressure should be controlled during welding to ensure welding quality and avoid false welding, false welding and other phenomena.