Ceramic capacitors (also known as porcelain capacitors or monolithic capacitors) are capacitors that use ceramic materials as the dielectric.
It uses ceramic material as a medium, and forms a dielectric film on the surface or inside of the ceramic as a dielectric. Ceramic capacitors come in various shapes, and common ones include tubular, round, rectangular, etc.
Origin of ceramic capacitors
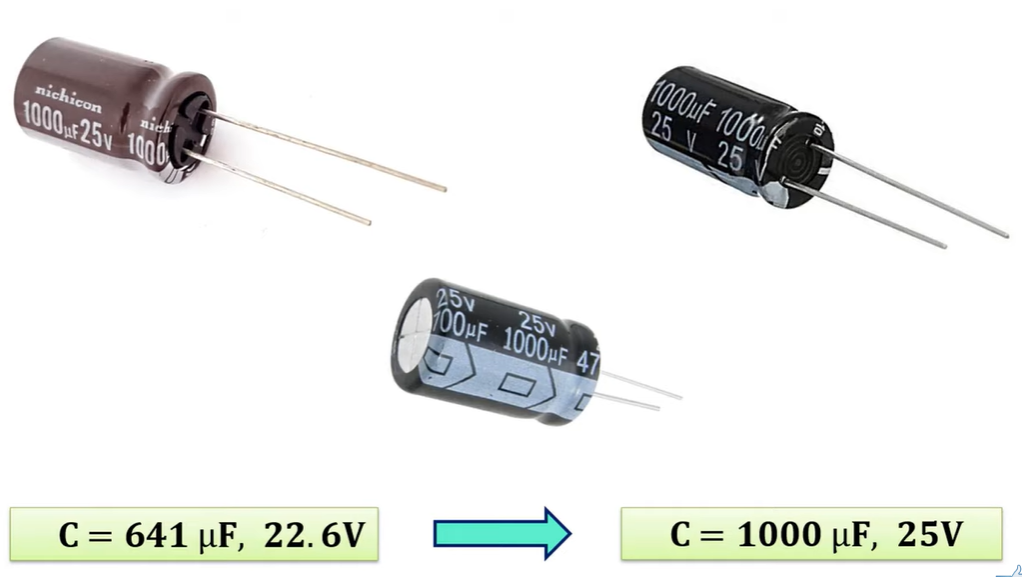
The origin of ceramic capacitors can be traced back to the early 20th century. The earliest ceramic capacitor was invented by Italian L. Lombardi in 1900. However, early ceramic capacitors had poor performance, low dielectric constant, and were easily affected by temperature and humidity. With the development of science and technology, people continue to explore and improve the materials and manufacturing processes of ceramic capacitors, gradually improving their performance and stability.
In the late 1930s, it was discovered that adding titanate could exponentially increase the dielectric constant of ceramic capacitors, thus creating cheaper porcelain dielectric capacitors. Around 1940, people discovered that barium titanate (BaTiO3) had insulating properties and could be used as a raw material for ceramic capacitors.
Barium titanate has the characteristics of high dielectric constant, low dielectric loss, high withstand voltage and excellent insulation properties. It is very suitable for use in small, high-precision electronic equipment.
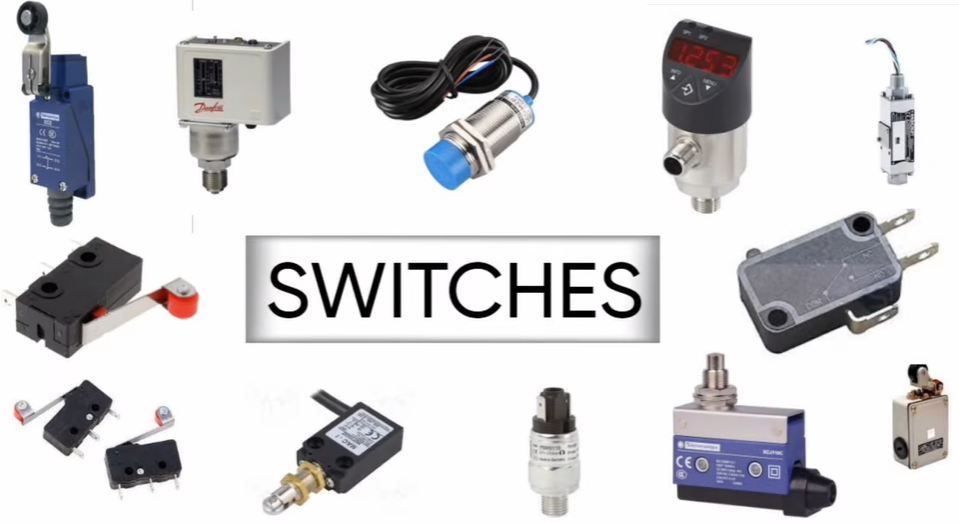
Since then, with the rapid development of the electronics industry, the demand for ceramic capacitors has continued to increase, and their manufacturing processes and technologies have been continuously improved and improved.
Nowadays, ceramic capacitors have become one of the indispensable components in electronic equipment and are widely used in communications, computers, home appliances, automobiles, aerospace and other fields.
When were ceramic capacitors introduced on the market?
Ceramic capacitors began to be used in military electronic equipment around 1940. With the advancement of hybrid ICs, computers, and portable electronic equipment, ceramic capacitors developed rapidly and became an indispensable component in electronic equipment. Around 1960, ceramic laminated capacitors began to be developed as commercial products and entered the market. The total number of ceramic dielectric capacitors now accounts for about 70% of the capacitor market.
Classification and definition of ceramic capacitors
Ceramic capacitors can be classified according to different standards. Here are some common classification methods:
- Classification by dielectric type: According to the characteristics of the dielectric material, ceramic capacitors can be divided into type I and type II. Type I ceramic capacitors are usually high dielectric constant and low loss capacitors, while type II ceramic capacitors have relatively low dielectric constant and high temperature coefficient.
- Classification according to temperature characteristics: The temperature coefficient of ceramic capacitors can be divided into three categories, namely Type 1, Type 2 and Type 3. Type 1 capacitors have a linear temperature coefficient, and the capacitance changes linearly with temperature; Type 2 capacitors have a nonlinear temperature coefficient, and the capacitance changes with temperature in a complex nonlinear relationship; Type 3 capacitors are usually semiconductor-type ceramics Capacitors have a high dielectric constant, but their capacitance changes little with temperature.
- Classification by packaging form: Ceramic capacitors can be divided into plug-in type and SMD type according to different packaging forms. Plug-in ceramic capacitors are larger in size and are suitable for situations where capacity requirements are not high; while chip-type ceramic capacitors are smaller in size and are suitable for dense integrated circuits in electronic equipment.
- Classification by voltage: According to the voltage that ceramic capacitors withstand, they can be divided into low-voltage, medium-voltage and high-voltage ceramic capacitors. Low-voltage ceramic capacitors are usually used in general situations, medium-voltage ceramic capacitors are suitable for situations that require higher stability, and high-voltage ceramic capacitors are suitable for situations that require higher withstand voltage.
Definition: Ceramic capacitor is a capacitor with ceramic material as the dielectric. It has the characteristics of high dielectric constant, low loss, high withstand voltage, etc. It is widely used in filtering, tuning, energy storage, coupling and other circuits in electronic equipment. According to different classification standards, ceramic capacitors can be divided into various types to meet the needs of different application scenarios.
Different definitions of application classes for ceramic capacitors
Definition regarding to IEC/EN 60384-1 and IEC/EN 60384-8/9/21/22 | Definition regarding to EIA RS-198 |
---|---|
Class 1 ceramic capacitors offer high stability and low losses for resonant circuit applications. | Class I (or written class 1) ceramic capacitors offer high stability and low losses for resonant circuit application |
Class 2 ceramic capacitors offer high volumetric efficiency for smoothing, by-pass, coupling and decoupling applications | Class II (or written class 2) ceramic capacitors offer high volumetric efficiency with change of capacitance lower than −15% to +15% and a temperature range greater than −55 °C to +125 °C, for smoothing, by-pass, coupling and decoupling applications |
Class 3 ceramic capacitors are barrier layer capacitors which are not standardized anymore | Class III (or written class 3) ceramic capacitors offer higher volumetric efficiency than EIA class II and typical change of capacitance by −22% to +56% over a lower temperature range of 10 °C to 55 °C. They can be substituted with EIA class 2- Y5U/Y5V or Z5U/Z5V capacitors |
– | Class IV (or written class 4) ceramic capacitors are barrier layer capacitors which are not standardized anymore |
Manufacturers, especially in the US, preferred Electronic Industries Alliance (EIA) standards. In many parts very similar to the IEC standard, the EIA RS-198 defines four application classes for ceramic capacitors.
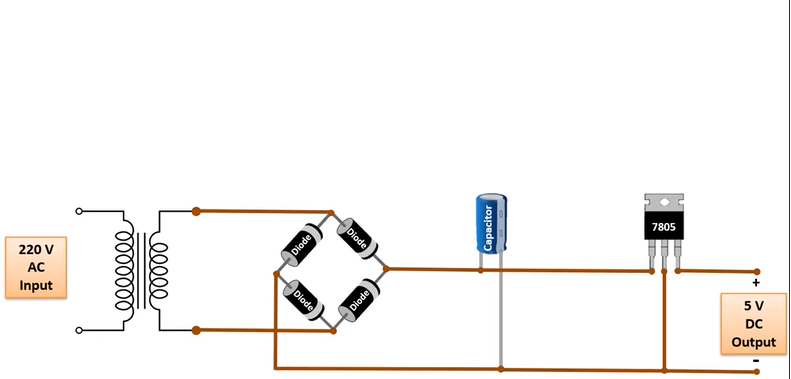
Advantages and Disadvantages of Ceramic Capacitors
The advantages of ceramic capacitors mainly include:
- High stability: Ceramic dielectric has a high dielectric constant and low dielectric loss, so ceramic capacitors have high stability.
- Good insulation: Ceramic dielectric has high insulation resistance and dielectric strength, which can ensure that the capacitor has good insulation performance.
- High voltage resistance: Ceramic dielectric has a high breakdown voltage, so ceramic capacitors can withstand high voltages.
- Large capacity: Ceramic dielectric has a high dielectric constant, so ceramic capacitors can be made into large-capacity capacitors.
- Low cost: The manufacturing cost of ceramic capacitors is relatively low, so they are cost-effective when mass produced.
However, ceramic capacitors also have some disadvantages:
- Unstable temperature coefficient: The temperature coefficient of ceramic capacitors is unstable, which means that the capacitance value may change with changes in temperature.
- Capacity changes with temperature: The capacity of ceramic capacitors changes with temperature, so you need to pay attention when using it in high or low temperature environments.
- Low mechanical strength: Ceramic dielectric is brittle, so ceramic capacitors are easily damaged when subjected to mechanical stress.
- Susceptible to voltage: Ceramic dielectric is prone to dielectric breakdown when subjected to high voltage, so you need to pay attention to the voltage limit when using it.
In summary, the advantages and disadvantages of ceramic capacitors are obvious, and it is necessary to choose whether to use ceramic capacitors based on specific application scenarios and requirements.
Ceramic capacitor symbol
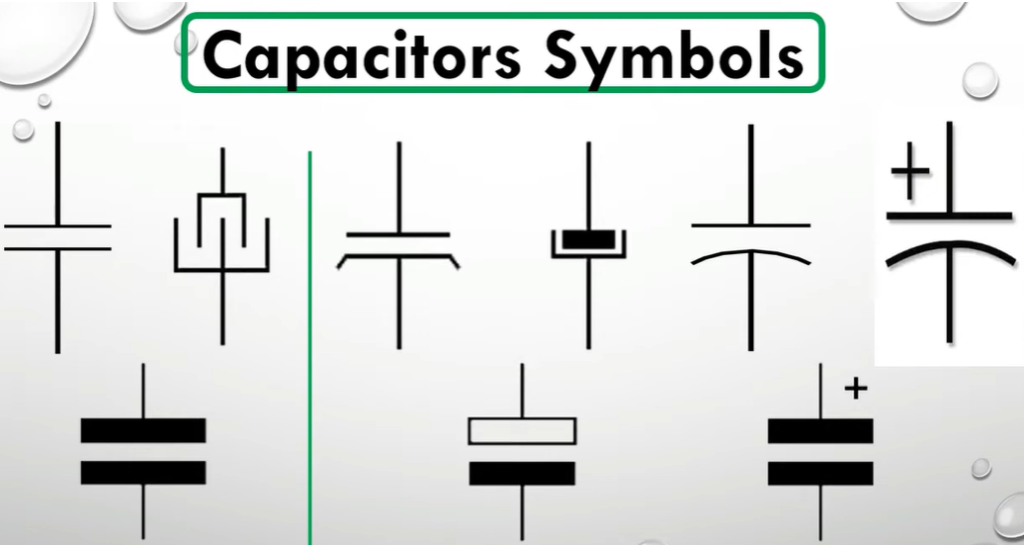
Working principle
The working principle of ceramic capacitors is based on the dielectric constant properties of ceramic materials. When a voltage is applied across both sides of a ceramic dielectric, an electric field is formed inside the dielectric, resulting in the accumulation of charges and an increase in the intensity of the electric field.
Due to the high dielectric constant of ceramic materials, a large amount of charges can be stored, thereby forming a high electric field strength. This electric field strength is related to the electrode area and voltage of the capacitor.
According to the formula C=εA/4πkd (where C is the capacitance, ε is the dielectric constant, A is the electrode area, and d is the electrode spacing), the capacity of the ceramic capacitor can be calculated .
In ceramic capacitors, the electrodes are usually made by printing or sputtering a metal film on a ceramic dielectric. After forming electrodes on the dielectric, connecting the two electrodes of the ceramic capacitor to a circuit allows charging and discharging via AC or DC signals. When a voltage is applied to the two electrodes of a ceramic capacitor, charges accumulate inside the medium to form an electric field. When the electric field reaches a certain intensity, an insulating layer will be formed on the surface of the medium, thereby preventing the flow of current. At this time, the ceramic capacitor behaves as an impedance element, and its impedance value is related to factors such as frequency, dielectric constant, electrode area, and electric field strength.
In practical applications, ceramic capacitors are usually used in bypass, filtering, coupling, resonance and other circuits. Due to its advantages such as high dielectric constant, low loss, high stability, and good high-frequency characteristics, ceramic capacitors have become one of the indispensable components in modern electronic equipment.
Chemical element composition of ceramic capacitors
Matter is composed of molecules, ions, and atoms. So what chemical elements are ceramic capacitors made of?
The chemical composition of ceramic capacitors varies depending on the manufacturing process and materials. Generally speaking, the raw materials of ceramic capacitors include high dielectric constant capacitor ceramics such as barium titanate titanium oxide, aluminum oxide, zinc oxide, manganese oxide and other substances.
Specifically, the ceramic dielectric of ceramic capacitors is mainly composed of a variety of oxides, such as barium titanate (BaTiO3), barium strontium titanate (BaSrTiO3), etc. In addition, some additives, such as glass frits, mineralizers, emulsions, etc., will be added to adjust the performance parameters of the medium.
During the manufacturing process, these materials undergo mixing, shaping, firing and other processes to form a ceramic dielectric diaphragm, and then electrode materials (such as nickel, silver, etc.) are coated on the diaphragm to form electrodes.
Structure and style
The structure of ceramic capacitors mainly consists of two parts: dielectric and electrodes. According to different classification standards, the structure and style of ceramic capacitors are also different.
According to the structural form, ceramic capacitors can be divided into various types such as disc, tubular, rectangular, sheet, and through-core. Among them, tubular and circular ceramic capacitors are widely used. In ceramic capacitors, the electrodes are usually made by printing or sputtering a metal film on a ceramic dielectric. The combination of dielectric and electrodes forms the basic structure of ceramic capacitors.
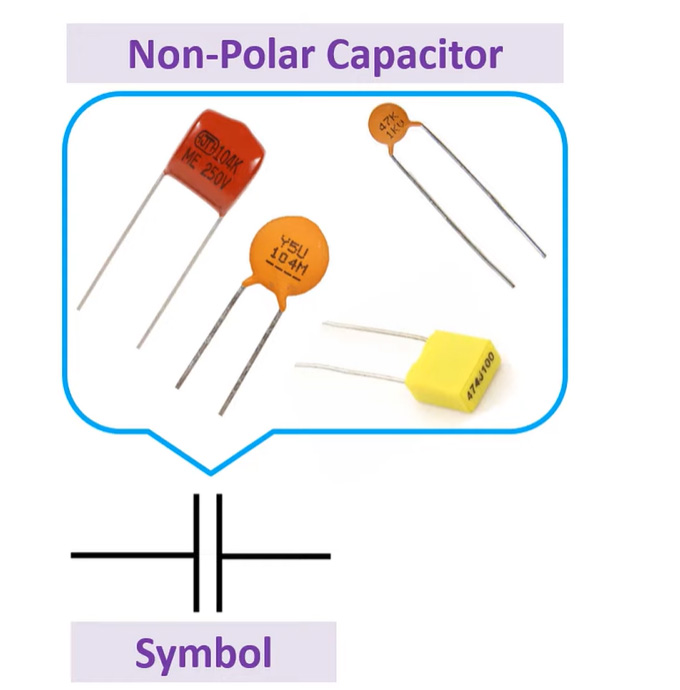
According to the classification of using voltage, ceramic capacitors can be divided into three types: high voltage, medium voltage and low voltage. Ceramic capacitors with different voltage levels also have different dielectric thickness and electrode material selections. In addition, ceramic capacitors can also be classified according to parameters such as temperature coefficient and dielectric constant.
In general, ceramic capacitors come in a variety of structures and styles, and can be selected according to different application scenarios and needs. In practical applications, it is necessary to select the appropriate type and specification of ceramic capacitors according to circuit requirements to achieve optimal performance and reliability.
Most Common Ceramic Capacitor Styles and Shapes
The most common style and shape of ceramic capacitors is chip ceramic capacitors, which are usually in the shape of a round or rectangular piece with an electrode pattern on the surface. SMD ceramic capacitors have the characteristics of miniaturization, high performance, and high reliability, and are commonly used in filtering, decoupling, signal processing and other circuits of various electronic equipment.
In addition to chip-type ceramic capacitors, there are also ceramic capacitors in various styles and shapes such as leaded type, axial type, and through-core type. These different types of ceramic capacitors each have their own characteristics and application scenarios, and they should be selected according to actual needs.
Electrical characteristics
The electrical characteristics of ceramic capacitors mainly include the following aspects:
- High insulation resistance and low loss: The ceramic dielectric itself has good insulation properties, so the insulation resistance of ceramic capacitors is very high, and it can maintain high insulation resistance in high temperature and high humidity environments. In addition, since the loss of the ceramic dielectric itself is small, the loss of the ceramic capacitor is also relatively small.
- Small capacity range: The capacity of ceramic capacitors is usually small, generally between 10-4 and 105μF, and is not suitable for applications requiring large capacity.
- Good stability: Ceramic capacitors have good stability, their capacity and loss change little with temperature and voltage, and they have a long service life and good reliability.
- Good high-frequency characteristics: Ceramic capacitors have small dielectric loss, so they have good high-frequency characteristics and are suitable for high-frequency circuits.
- High voltage and high temperature resistance: The dielectric material of ceramic capacitors has high dielectric constant and insulation properties, so it can withstand high voltage and temperature.
To sum up, the electrical characteristics of ceramic capacitors make them one of the widely used components in electronic equipment. They are often used in bypass, filtering, coupling, resonance and other circuits.
International standards
International standards for ceramic capacitors include the following:
- IEC 60384-1, which specifies general requirements and test methods for ceramic capacitors.
- IEC 60384-2, this standard specifies the requirements and test methods for ceramic capacitors classified by capacity.
- IEC 60384-3, this standard specifies the requirements and test methods for ceramic capacitors classified by media.
- IEC 60384-4, this standard specifies the requirements and test methods for ceramic capacitors classified by electrodes.
- IEC 60384-5, this standard specifies the requirements and test methods for ceramic capacitors classified by use.
In addition, the standards of ceramic capacitors in various countries and regions may also be different, so in practical applications, it is necessary to pay attention to the standard requirements of different countries and regions.
Replacement product
Substitute products for ceramic capacitors mainly include plastic film capacitors, aluminum electrolytic capacitors and other types of capacitors.
Among them, plastic film capacitors have the advantages of high stability, low temperature drift, large capacity, and high precision, and are widely used in high-frequency and high-voltage circuits. At the same time, the price of plastic film capacitors is relatively low and suitable for a large number of applications. Aluminum electrolytic capacitors have the advantages of large capacity, high voltage, low distortion, etc., but their capacity changes greatly with time and temperature, their ultimate operating temperature is also low, and their relatively slow response time also limits their use in high-speed computer boards, high-speed computers, etc. Applications in signal circuits and other fields.
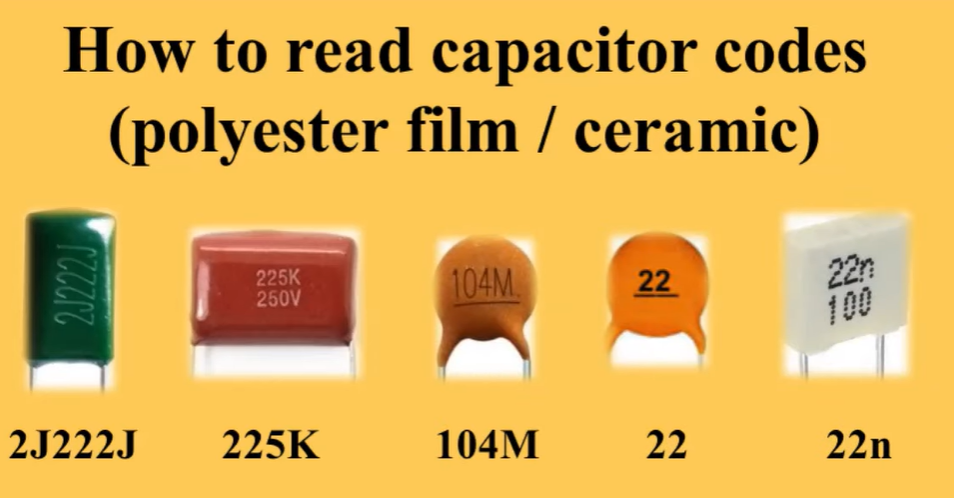
In addition, other types of capacitors such as tantalum capacitors and electrolytic capacitors may also be used in certain circuits for specific purposes.
When choosing alternative products, you need to choose based on specific application scenarios and needs, and compare the performance, price, reliability and other factors of different products to determine the most suitable alternative product.
Manufacturing process
The manufacturing process of ceramic capacitors mainly includes the following steps:
- Ingredients: According to production requirements, weigh various raw materials in proportion, add them to the mixer and mix them evenly to obtain the ceramic green body to be pressed.
- Film making: Put the mixed raw materials into a mold and press them under a certain temperature and pressure to obtain a ceramic green diaphragm.
- Firing: Put the prepared ceramic green diaphragm into a high-temperature furnace for firing, so that the ceramic dielectric material is completely sintered and dense, forming a ceramic dielectric diaphragm with certain mechanical strength and electrical properties.
- Electrode coating: Coating a layer of metal electrode material on the surface of the ceramic dielectric diaphragm, usually by electroplating or sputtering.
- Firing the electrode: Put the ceramic dielectric diaphragm coated with the electrode into a high-temperature furnace for firing, so that the metal electrode material and the ceramic dielectric material are completely fused together to form an electrode layer with good conductivity.
- Appearance inspection and performance testing: Conduct appearance inspection and performance testing on the fired ceramic capacitors to check whether there are defects, bubbles, cracks and other problems, and test whether their electrical performance meets the requirements.
- Packaging: Pack qualified ceramic capacitors for storage, transportation and use.
In the manufacturing process of ceramic capacitors, process links such as batching, film making, and firing have a great impact on the performance and quality of the product. It is necessary to strictly control the process parameters and the quality of raw materials.
At the same time, in order to improve the performance and reliability of ceramic capacitors, some special manufacturing processes can be used, such as using ceramic materials with high dielectric constants, adding reinforcing materials, surface treatments, etc.
What are ceramic capacitors made of?
Ceramic capacitors are made of ceramic materials and electrode materials. Ceramic material is the capacitor dielectric, which determines the electrical and mechanical properties of the capacitor. Commonly used ceramic materials include barium titanate, barium strontium titanate, alumina, etc., which have high dielectric constant, stable dielectric properties and good mechanical strength. Electrode materials usually include conductive metal materials such as brass and stainless steel, which are used to form electrode layers on ceramic media to achieve the transmission and storage of electrical signals.
The manufacturing process of ceramic capacitors mainly includes steps such as ingredients, film making, firing, electrode coating, electrode firing, appearance inspection and performance testing. The ingredients are to weigh various raw materials in proportion and mix them evenly to obtain a ceramic green body to be pressed. Film making is to put the mixed raw materials into a mold and press them under a certain temperature and pressure to obtain a ceramic green diaphragm.
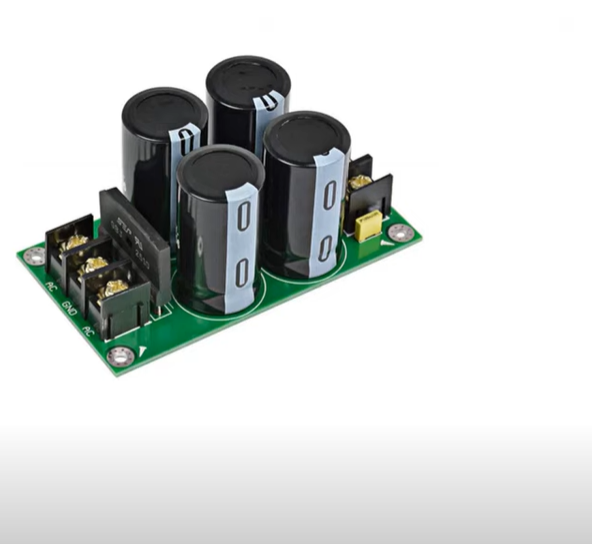
Firing is to put the prepared ceramic green diaphragm into a high-temperature furnace for firing, so that the ceramic dielectric material is completely sintered and dense, forming a ceramic dielectric diaphragm with certain mechanical strength and electrical properties. Electrode coating is to coat a layer of metal electrode material on the surface of a ceramic dielectric diaphragm, usually by electroplating or sputtering.
Firing the electrode is to put the ceramic dielectric diaphragm coated with the electrode into a high-temperature furnace for firing, so that the metal electrode material and the ceramic dielectric material are completely fused together to form an electrode layer with good conductive properties. Appearance inspection and performance testing is to conduct appearance inspection and performance testing on fired ceramic capacitors to check whether there are defects, bubbles, cracks and other problems, and to test whether their electrical performance meets the requirements. Packaging is to package qualified ceramic capacitors for storage, transportation and use.
In general, the manufacturing of ceramic capacitors requires strict control of process parameters and raw material quality to ensure product performance and reliability.
Application areas
The application of ceramic capacitors can be analyzed specifically according to different fields.
- Consumer electronics field: Ceramic capacitors are widely used in various consumer electronics products, such as mobile phones, tablet computers, digital cameras, etc. The market size of these downstream industries is huge and the demand for ceramic capacitors is strong, which provides strong support for the development of the industry.
- Communication field: Ceramic capacitors play an important role in high-frequency signal transmission and filter circuits, so they are widely used in communication equipment, such as mobile phones, wireless routers, satellite communication equipment, etc.
- Automotive electronics field: With the improvement of automobile electronics level, the application of ceramic capacitors is also expanding. In automotive circuits, ceramic capacitors can be used for charge storage, filtering and other functions to ensure the reliable operation of automotive electronic equipment. Especially with the development of smart cars, the requirements for the reliability and high temperature resistance of electronic components are getting higher and higher, which provides broad prospects for the application of ceramic capacitors in automotive electronic systems.
- Medical equipment field: Ceramic capacitors are also widely used in medical equipment. For example, in electronic blood pressure monitors, electronic thermometers and other equipment, they can play a role in filtering and voltage stabilization to improve the accuracy and stability of the equipment.
- Industrial automation field: Ceramic capacitors also play an important role in automation equipment.
In addition, the ceramic capacitor industry has also benefited from factors such as continued technological advancement, industrial transfer dividends, and improved policy environment. These factors have provided strong support for the development of the industry.
In general, the application market of ceramic capacitors is constantly growing, especially in the fields of communication equipment, automotive electronics, medical equipment and industrial automation. In the future, with the advancement of technology and changes in market demand, the application fields and market size of ceramic capacitors will will continue to expand.
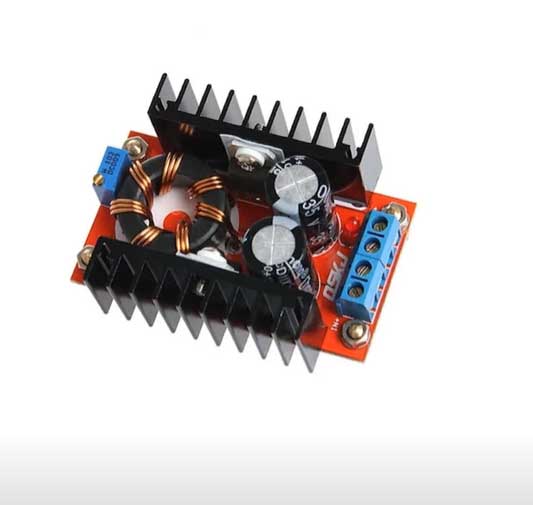
Manufacturers and products
Manufacturers and products of ceramic capacitors are as follows:
- Murata Manufacturing Co., Ltd.: The world’s leading manufacturer of electronic components, mainly producing ceramic capacitors and other electronic components.
- TAIYO YUDEN: A Japanese company whose That’s discs have been famous in the CD era. Its main products include ceramic capacitors.
- TDK: An electronic industry brand whose main products include capacitors, inductors, transformers, radio frequency devices, optical devices, electromagnetic interference suppression devices, power modules, sensors, magnetic cores, etc.
- Kemet: A world-renowned capacitor manufacturer founded in 1919 and headquartered in the United States.
- WALSIN (Huaxin Technology): A Taiwanese company with a capital of 5.17 billion yuan. Its main products include passive components (multilayer ceramic capacitors, chip resistors, inductors and magnetic beads).
- Guangdong Hecotech Industrial Co., Ltd.: Founded in 1992, it is the world’s leading semiconductor production service provider and a nationally certified high-tech enterprise. It initially focused on the R&D and production of passive components: chip resistors and chip capacitors.
- Songtian Electronics: China’s leading professional manufacturer of ceramic capacitors, film capacitors, varistors, and thermistors, focusing on the fields of electronic complete machines such as power supplies, home appliances, and digital appliances, and energy-saving lighting, and is committed to providing professional support to our customers. One-stop service.
- Fenghua Hi-Tech: China’s largest passive component R&D and manufacturing company. Its main ceramic capacitor products include multilayer ceramic capacitors. It has full industry production capabilities from materials, processes to new technology research and development, with a monthly production capacity of 15-20 billion pieces.
In addition, there are also well-known electronic component manufacturers such as TDK Co., Ltd. For more information, it is recommended to visit the official website of the relevant brand.
Ceramic Capacitor FAQs
Overvoltage may cause breakdown of ceramic capacitors, resulting in their destruction. Therefore, when using ceramic capacitors, ensure that their operating voltage does not exceed the rated voltage to avoid overvoltage.
The capacitance change of ceramic capacitors may be related to factors such as its manufacturing process, temperature, humidity, etc. If the operating environment temperature is too high or the humidity is too high, the capacity of the ceramic capacitor may also change.
Ceramic capacitors will not leak. If you encounter this situation, it may be due to other reasons, such as cracks inside the capacitor or aging of the sealing material. Therefore, during use, attention should be paid to checking whether the capacitor is leaking and dealing with it in time.
The service life of ceramic capacitors is related to factors such as its manufacturing process, usage environment, and working voltage. If the use environment is harsh, the working voltage is too high, or the manufacturing process is poor, the service life of ceramic capacitors may be shortened. Therefore, during use, care should be taken to protect the capacitor to avoid overvoltage, overcurrent, overheating, etc.