The MP86956 monolithic half-bridge chip is an integrated circuit produced by the American Core Source (MPS). This chip is widely used in various electronic devices that require half-bridge drive, such as inverters, motor drives, etc.
The MP86956 monolithic half-bridge chip has the characteristics of high integration, low power consumption, and high performance, which can effectively improve the efficiency and stability of electronic equipment.
MP86956 monolithic half-bridge chip is a powerful motor drive control chip specially designed for half-bridge circuits.
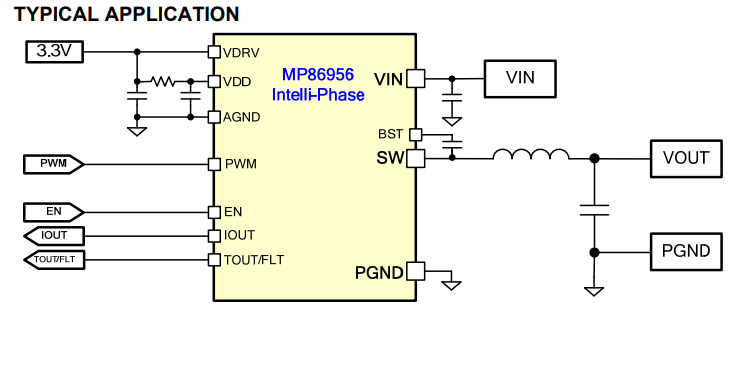
It integrates logic gates, dead time control and protection functions to make motor drive circuit design simpler. Through the built-in logic gate, users can easily control the forward, reverse and stop of the motor to achieve precise motion control.
The MP86956 is a monolithic half-bridge chip with built-in power MOSFETs and gate drivers. It achieves 70A continuous output current (IOUT) over a wide input voltage range.
Dead time control can effectively prevent direct short circuit between the upper and lower bridge arms and protect the safety of the motor and circuit. In addition, MP86956 also has various protection functions such as over-current protection and over-temperature protection, which further improves the stability and reliability of the system.
Using the MP86956 chip, users can easily build an efficient and stable half-bridge drive circuit, which is widely used in motor drive, solenoid valve control and other fields.
Advantages of MP86956 monolithic half-bridge chip
The advantages of the MP86956 monolithic half-bridge chip include the following aspects:
- High efficiency: This chip adopts optimized circuit design and advanced process technology, which can efficiently control the motor drive, reduce energy loss, and improve the energy efficiency of the overall equipment.
- Simple and easy to use: The MP86956 chip integrates logic gates, dead time control and protection functions, simplifying the design of the motor drive circuit and reducing the difficulty of use. Users only need simple peripheral components to build an efficient and stable half-bridge drive circuit.
- High stability: The chip has multiple protection functions such as overcurrent protection and overheating protection, and can automatically detect and respond to abnormal situations to ensure stable operation of the system. At the same time, after strict quality control and reliability testing, the MP86956 chip has high stability and reliability.
- Miniaturization: The MP86956 chip adopts a compact package, which helps reduce the size of the motor drive control system, making it more suitable for applications with limited space.
- High integration: Compared with traditional motor drive circuits built with discrete components, the MP86956 chip integrates multiple functions into one, reducing the complexity of the circuit and improving integration. This helps simplify circuit design, reduce manufacturing costs, and reduce board size.
- Wide applicability: MP86956 chip can be widely used in various fields that require half-bridge drive circuits, such as motor drive, solenoid valve control, etc. Its versatile features help simplify stocking and inventory management, reducing production and operating costs.
MP86956 monolithic half-bridge chip parameters

The parameters of the MP86956 monolithic half-bridge chip include the following aspects:
- Working voltage: The chip’s working voltage range is 10V to 30V, which is sufficient to meet the needs of most motor driving scenarios.
- Maximum output current: The maximum output current of the MP86956 chip can reach 70A, which can drive medium-power motors.
- Dead time control: The chip has a dead time control function, which can prevent the upper and lower bridge arms from being short-circuited and protect the safety of the motor and circuit.
- Protection function: The MP86956 chip has multiple protection functions such as overcurrent protection and overheating protection, which can improve the stability and reliability of the system.
- Package form: The chip is packaged in LGA-41 (5mmx6mm) and TLGA-41 (5mmx6mm), which is small in size and easy to integrate into the motor drive circuit.
MP86956 Manufacturer MPS
Core Source Systems (MPS) is a world-renowned high-performance analog semiconductor company headquartered in San Jose, California, USA.
Founded in 1997, the company has three core competitive advantages: years of system and application-level technology accumulation, first-class analog integrated circuit design capabilities, and independent innovative process technology. These core competitiveness enable the company to produce highly integrated single-chip Chip products provide customers with high-efficiency, low-cost solutions.
What are the application scenarios of MP86956 monolithic half-bridge chip?
The application scenarios of MP86956 monolithic half-bridge chip mainly include the following aspects:
- Motor drive: MP86956 chip can be widely used in drive control of DC motors, stepper motors, servo motors and other motors. Through this chip, users can easily realize control functions such as forward and reverse rotation, speed regulation and positioning of the motor.
- Solenoid valve control: Solenoid valves are commonly used components in industrial control and fluid control. The MP86956 chip can be used to drive and control solenoid valves. Through this chip, users can achieve precise control of the solenoid valve, thereby controlling the flow rate, pressure and other parameters of the fluid medium.
- Automatic control system: MP86956 chip can be used in various automatic control systems, such as smart home control systems, industrial automation production line control systems, etc. In these systems, the chip can be used as an actuator to implement various automated operations and controls.
- Robotics: In the field of robotics, the MP86956 chip can be used in robot joint drives, mobile platform drives, etc. Through this chip, the robot can achieve high-precision and fast motion control.
- Electronic door lock system: The electronic door lock system needs to realize the drive and control of the motor to open and close the door. The MP86956 chip can be used for motor drive and control of electronic door lock systems to improve the stability and reliability of the system.
The MP86956 monolithic half-bridge chip has a wide range of application scenarios and can be applied to fields such as motor drive, solenoid valve control, automatic control systems, robotics, and electronic door lock systems. Its advantages of high efficiency, ease of use, high stability, miniaturization, high integration and wide applicability make this chip an ideal choice in these fields.
Monolithic half-bridge chip MP86956 product manual download
MP86956 Monolithic Half-Bridge Chip Datasheet Manual:
MP86956 FAQs
A half-bridge driver is a circuit used to control the movement of a motor or other load. It converts the supply voltage to a voltage suitable for the load and provides the necessary current. This type of driver is commonly used for DC motors, stepper motors, and other loads that require precise control.
The half-bridge driver realizes the speed and steering control of the motor by controlling the on and off of the two switching tubes (M1, M2). The control signal can also be PWM modulated.
The MP86956 monolithic half-bridge chip is a highly integrated, high-performance half-bridge driver chip with the following characteristics:
High integration: Integrates all functional modules required for the half-bridge drive circuit, such as input logic control, dead time control, power supply, etc., greatly simplifying circuit design.
High performance: It has fast response speed and low noise performance, and can provide accurate driving signals to ensure the stable operation of motors or other loads.
Convenient motor control: Supports PWM (pulse width modulation) and complementary PWM control methods to facilitate control of motor speed and direction.
Complete protection functions: Built-in over-current protection, over-temperature protection and other protection functions ensure that the chip can automatically protect and prevent damage under abnormal circumstances.
Low power consumption: The low-power consumption design effectively reduces the power consumption of the motor control system and extends the battery life of the device.
The MP86956 monolithic half-bridge chip is widely used in the field of motor control, such as DC motors, stepper motors, servo motors, etc. By using this chip with appropriate power tubes and drive circuits, precise control and efficient operation of the motor can be achieved. At the same time, due to its low power consumption characteristics, the chip is also suitable for battery-powered mobile devices.
Using the MP86956 monolithic half-bridge chip requires following certain steps and precautions. First, you need to understand the basic specifications and pin definitions of the chip, and correctly connect the input signals and control signals. Secondly, select the appropriate power tube and drive circuit according to the type of motor and drive requirements. At the same time, attention needs to be paid to the connection of the power supply and ground wire to ensure stable power supply and low noise. During use, you also need to pay attention to safety issues such as over-current protection and over-temperature protection to avoid damage to the chip and motor due to abnormal conditions.
Compared with traditional discrete driver circuits, the MP86956 monolithic half-bridge chip has obvious advantages. First, high integration simplifies circuit design, reduces the number of components and wiring complexity, and reduces costs and error rates. Secondly, the high-performance drive signal ensures the stable operation of the motor and improves the system’s response speed and control accuracy. In addition, complete protection functions enhance the reliability and security of the system. Finally, the low power consumption makes the chip suitable for a variety of battery-powered applications.
When using the MP86956 monolithic half-bridge chip, you may encounter some problems, such as unstable driving signals, loud motor operation, overcurrent or overtemperature, etc. Corresponding solutions can be taken to address these problems. First, ensure the stability and correctness of the input signal to avoid signal interference and false triggering. Secondly, adjust the parameters of the drive signal according to the characteristics of the motor and the operating environment, such as dead time, PWM duty cycle, etc. At the same time, check whether the connection between the power supply and the ground wire is stable and reliable to reduce the impact of power supply noise on the drive signal. For overcurrent or overtemperature problems, you need to check whether the motor load is normal and whether the heat dissipation is good. If the abnormality still cannot be resolved, it is recommended to refer to the chip’s technical manual or seek professional technical support.