LKS32MC051C6T8 is a walking controller specially designed for handling robots. It integrates efficient motion control algorithms and powerful driving capabilities to ensure that the robot walks accurately and stably and completes tasks quickly.
Whether it is speed control, position positioning or path planning, LKS32MC051C6T8 can provide excellent performance and is an ideal choice for efficient automated handling.
Introduction
With the continuous development of industrial automation and intelligent manufacturing, handling robots are increasingly used in production lines, warehouse management, logistics and distribution and other fields. As the core component of a handling robot, the walking controller plays a vital role in the robot’s motion performance, stability and accuracy.
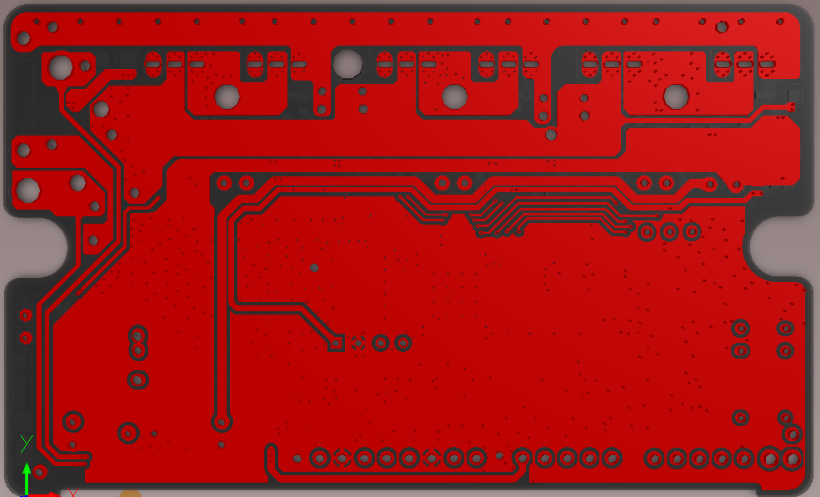
LKS32MC051C6T8 is a powerful 32-bit microcontroller with high-speed processing capabilities and rich peripheral interfaces, suitable for various automation and robot control applications. This article will introduce in detail the working principle, hardware design, software algorithm and control strategy of the handling robot walking controller based on LKS32MC051C6T8.
Working principle of handling robot walking controller
The handling robot walking controller based on LKS32MC051C6T8 receives input signals from sensors, encoders and remote controls, and outputs corresponding control signals to drive motors, servos and other actuators according to preset control algorithms and programs. Specifically, the controller obtains the motor speed and direction information through the encoder, obtains the robot attitude information through the gyroscope and accelerometer, receives operating instructions through the remote control, calculates the control signal based on the kinematic model and control algorithm, and outputs it to the motor driver. and steering gear driver to achieve precise control of the robot.
Hardware design of LKS32MC051C6T8 handling robot
The hardware design of the handling robot walking controller based on LKS32MC051C6T8 mainly includes microcontroller, power module, sensor interface, motor driver and communication interface. The microcontroller is the core of the entire controller and is responsible for processing input signals, executing control algorithms and outputting control signals. The power module provides a stable power supply to the controller to ensure the normal operation of the controller. The sensor interface is used to connect sensors to obtain robot and environmental information. The motor driver is used to drive the walking motor to realize the forward, backward, steering and other actions of the robot. The communication interface is used for data exchange and communication with other devices.
Software algorithm
The software algorithm is an important part of the handling robot walking controller based on LKS32MC051C6T8. The control algorithm includes kinematic model, control strategy and fault diagnosis. The kinematic model is used to describe the motion characteristics and trajectory planning of the robot, the control strategy is used to achieve precise control and stability adjustment of the robot, and fault diagnosis is used to detect and diagnose faults or abnormal conditions in the control system. During the implementation of software algorithms, issues such as real-time performance, reliability, and scalability need to be considered.
Control Strategy
The control strategy of the handling robot walking controller based on LKS32MC051C6T8 mainly includes speed control, direction control and attitude control. Speed control is used to adjust the robot’s traveling speed, direction control is used to realize the left and right steering and U-turn movements of the robot, and attitude control is used to maintain the balance and stability of the robot. During the implementation of the control strategy, issues such as the robot’s motion performance, stability, and safety need to be comprehensively considered.
Experimentation and verification
In order to verify the performance and reliability of the handling robot walking controller based on LKS32MC051C6T8, experiments and tests are required. The experimental content includes the robot’s motion performance test, stability test and environmental adaptability test. Experimental results show that the controller can achieve high-precision and high-stability motion control, and has good environmental adaptability and safety.
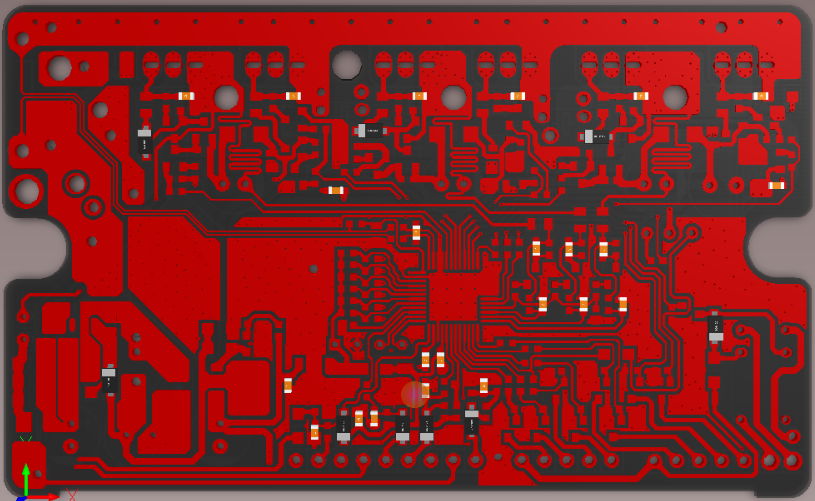
Conclusion and Outlook
The handling robot walking controller based on LKS32MC051C6T8 has the characteristics of high performance, programmability, rich peripheral interfaces, modular design, safety and easy integration.
In practical applications, the controller can achieve efficient and accurate handling operations, improve production efficiency and reduce costs.
In the future, with the continuous development and advancement of technology, the handling robot walking controller based on LKS32MC051C6T8 will be applied and developed in more fields.
At the same time, it is necessary to further research and improve the performance and functions of the controller, and improve its stability and reliability to adapt to more complex and harsh application environments.
FAQs
LKS32MC051C6T8 is a 32-bit microcontroller produced by LKS Company. It has high performance, low power consumption, high-speed processing and other characteristics, and is suitable for various automation and robot control applications.
The controller has the following features:
High performance: The LKS32MC051C6T8 microcontroller has high-speed processing capabilities and can quickly respond to control signals and process complex control algorithms to improve the movement performance and stability of the handling robot.
Programmability: Supports multiple programming languages, such as C/C++, etc., making it convenient for developers to carry out software programming and algorithm development. It also supports online programming and debugging to facilitate function expansion and upgrade of the controller.
Rich peripheral interfaces: Equipped with rich peripheral interfaces, such as UART, SPI, I2C, etc., to facilitate communication and control with other devices. These interfaces can be used to connect sensors, actuators and other control systems to achieve comprehensive control and intelligent management of handling robots.
Modular design: Modular design is adopted to modularize different functions for easy combination and expansion. This design method can improve the maintainability and scalability of the controller, making it easy to customize and upgrade according to different handling task requirements.
Safety: It has complete safety protection mechanisms, such as over-current protection, over-voltage protection and under-voltage protection, etc. to ensure the safety and reliability of the handling robot during operation. At the same time, software algorithms are used to achieve stability and reliability control, reducing the jitter and errors of the robot during walking.
Easy to integrate: Standardized hardware interfaces and communication protocols are used to facilitate integration and interconnection with other control systems. This design method can improve the configurability and scalability of the handling robot and facilitate the implementation of more intelligent handling solutions.
The controller receives input signals from sensors, encoders, remote controls, etc., and outputs corresponding control signals to drive actuators such as motors and servos based on preset control algorithms and programs. Specifically, the controller obtains the motor speed and direction information through the encoder, obtains the robot attitude information through the gyroscope and accelerometer, receives operating instructions through the remote control, calculates the control signal based on the kinematic model and control algorithm, and outputs it to the motor driver. and steering gear driver to achieve precise control of the robot.
It mainly includes microcontroller, power module, sensor interface, motor driver and communication interface. The microcontroller is the core of the entire controller and is responsible for processing input signals, executing control algorithms and outputting control signals. The power module provides a stable power supply to the controller to ensure the normal operation of the controller. The sensor interface is used to connect sensors to obtain robot and environmental information. The motor driver is used to drive the walking motor to realize the forward, backward, steering and other actions of the robot. The communication interface is used for data exchange and communication with other devices.
It mainly includes kinematic model, control strategy and fault diagnosis. The kinematic model is used to describe the motion characteristics and trajectory planning of the robot, the control strategy is used to achieve precise control and stability adjustment of the robot, and fault diagnosis is used to detect and diagnose faults or abnormal conditions in the control system. During the implementation of software algorithms, issues such as real-time performance, reliability, and scalability need to be considered.
It mainly includes speed control, direction control and attitude control. Speed control is used to adjust the robot’s traveling speed, direction control is used to realize the left and right steering and U-turn movements of the robot, and attitude control is used to maintain the balance and stability of the robot. During the implementation of the control strategy, issues such as the robot’s motion performance, stability, and safety need to be comprehensively considered.
Experimentation and testing are required. The experimental content includes the robot’s motion performance test, stability test and environmental adaptability test. Experimental results show that the controller can achieve high-precision and high-stability motion control, and has good environmental adaptability and safety.