The principle of insertion method of electronic components is an important part of the electronic assembly process, involving many aspects such as circuit board design, component selection and layout, and the efficiency of the production process.
The following is a detailed introduction to the principles of electronic component insertion.
Principles of component insertion
- Polarity of components: When inserting components, the polarity of each component must be clear based on the circuit diagram and component specification table, and the correct direction must be ensured for installation.
- Marking of components: All installed components must be clearly marked. These markings include component numbers, specifications, directions, etc. to facilitate subsequent debugging and maintenance.
- Layout of components: The layout of components should be as uniform and symmetrical as possible in accordance with the requirements of circuit design to improve the overall aesthetics and reduce thermal stress caused by uneven heat distribution.
- Fixing of components: Components should be fixed on the PCB board by welding, mechanical clamping, gluing, etc. During the fixing process, avoid applying excessive pressure or torque to the components to avoid damage.
- Spacing of components: The spacing between components should be determined according to the requirements of the circuit and the production process. Proper spacing ensures the electrical performance of the circuit board and the operability of the production process.
- Identification of components: Components should be clearly marked, including component numbers, specifications, directions, etc., to facilitate subsequent debugging and maintenance.
Choice of insertion method
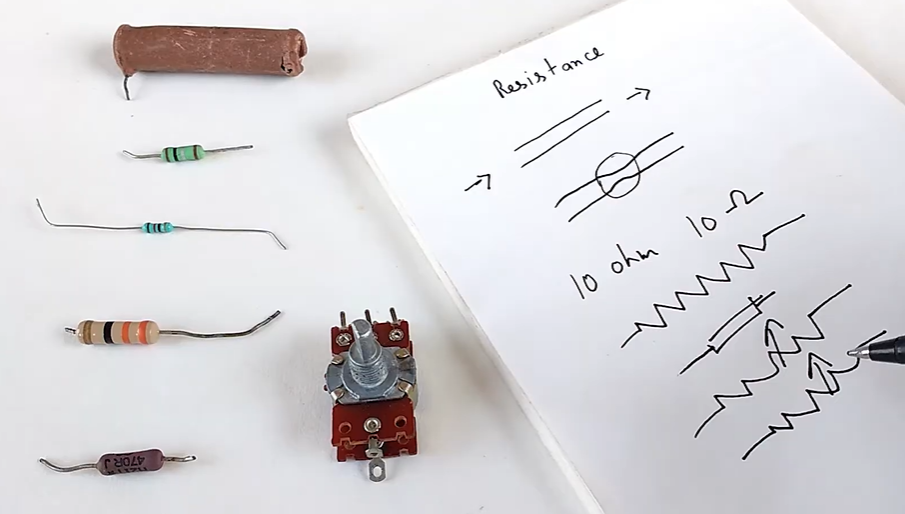
- Manual insertion and automatic insertion: According to the requirements of production scale and automation level, you can choose manual insertion or automatic insertion. Manual insertion is more flexible and suitable for small batch production and maintenance; automatic insertion is more efficient and suitable for mass production.
- Direct plug-in and surface mount: There are two methods of component insertion: direct plug-in and surface mount. In-line components can be directly inserted into the holes of the PCB board; surface mount components are directly attached to the surface of the PCB board. Surface mounting has the advantages of small size, light weight, and high reliability, but the manufacturing cost is high.
- Ordinary plug-in and special plug-in: For some circuit boards with special requirements, such as high-density and high-reliability aerospace fields, special plug-in methods are required, such as vertical installation, flip-chip welding, etc.
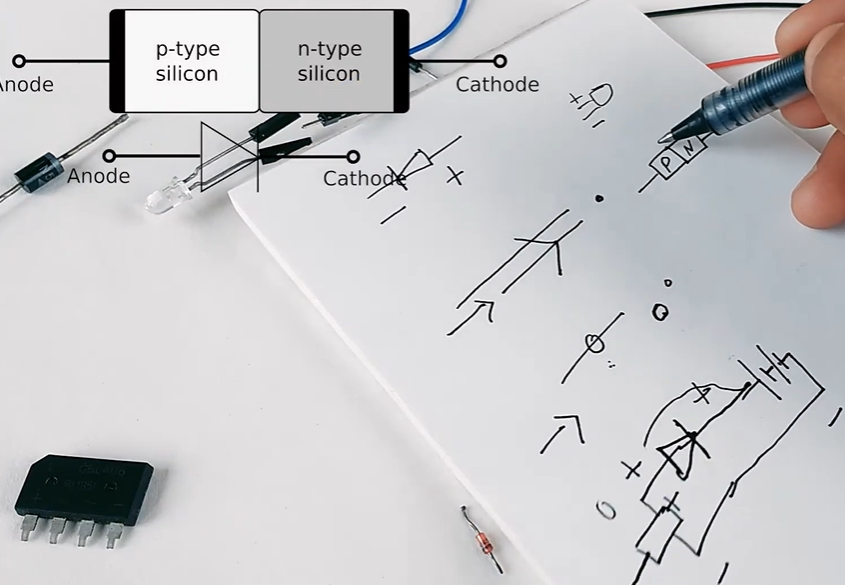
Principles and key points of instrumentation
- Ensure electrical performance: When inserting components, ensure that the electrical performance of the circuit board is met. For example, for some high-frequency signal lines, avoid excessively long traces or right-angle bends to reduce signal loss and noise.
- Heat dissipation design: For some high-power components, heat dissipation issues need to be considered. Good heat dissipation can be ensured by properly arranging the radiator or increasing the spacing between components.
- Prevent electromagnetic interference: When inserting components, electromagnetic interference issues should be considered. The impact of electromagnetic interference on circuit performance can be reduced by rationally arranging components and adding shielding measures.
- Convenient maintenance and testing: When inserting components, subsequent maintenance and testing should be considered. Test points can be set up and clearly marked to facilitate maintenance personnel for inspection and repair.
- Consider manufacturing costs: On the premise of meeting performance requirements, manufacturing costs should be reduced as much as possible. This can be achieved by optimizing circuit design, selecting appropriate components and insertion methods.
Practical application case analysis
In actual applications, it is necessary to choose the appropriate insertion method according to specific application scenarios and needs. For example, for some aerospace fields with high reliability requirements, special insertion methods can be used to ensure the performance and reliability of circuit boards; for some consumer electronics products, automated insertion methods can be used to improve production efficiency.
To sum up, the principle of insertion method of electronic components is an important part of the electronic assembly process. During the plug-in process, certain principles and key points need to be followed, and multiple factors such as electrical performance, reliability, and manufacturing cost must be comprehensively considered. The correct insertion method can ensure the performance and reliability of the circuit board, improve production efficiency, and reduce maintenance costs.
Frequently Asked Questions on the Principles of Inserting Electronic Components
Before electronic components are inserted, the printed circuit board must be cleaned to remove impurities such as dirt, dust, and oxides on the surface. These impurities may cause short circuits, open circuits on the circuit board, or affect the stability of components.
The pins of electronic components cannot be bent, because bent pins may short-circuit or have poor contact with adjacent pins, causing circuit failure. In addition, lead bending can affect the mechanical properties and reliability of components.
When inserting electronic components, ensure that the insertion direction is correct and the force is moderate, and avoid using brute force. At the same time, the principles of first small then large, first low then high, first light then heavy should be followed to avoid damage to other installed components.
In order to ensure the stability of electronic component insertion, the insertion should be carried out according to a reasonable layout and arrangement to ensure that each component can be firmly fixed on the printed circuit board. At the same time, an appropriate amount of solder should be used and the welding quality should be ensured to prevent problems such as desoldering and virtual soldering.
Before insertion, the quality of electronic components should be checked. Detection can be done through visual inspection, measurement and testing. If necessary, use a magnifying glass or microscope for a more detailed inspection. If there are any damaged or unqualified components, they should be replaced in time.