Regarding the control of the particle size distribution and specific surface area of magnesium oxide, this is a complex issue involving multiple fields such as materials science, chemical engineering and nanotechnology.
The following will introduce in detail how to control the particle size distribution and specific surface area of magnesium oxide.
Control of particle size distribution
Particle size distribution is one of the important parameters of magnesium oxide performance, which has a significant impact on the dispersion, reactivity and performance of the final product. The methods for controlling the particle size distribution of magnesium oxide mainly include the following aspects:
Selecting suitable raw materials
- The purity, particle size and crystal structure of the raw materials directly affect the particle size distribution of the final product. Therefore, high-purity and uniformly sized raw materials should be selected, such as high-purity magnesium chloride, magnesium sulfate, etc.
Optimizing the preparation process
- Precipitation method: By controlling the addition rate of the precipitant, the reaction temperature, the stirring intensity and other conditions, the nucleation and growth process of magnesium oxide can be regulated, thereby controlling the particle size distribution. For example, slowly adding the precipitant is conducive to the formation of small-sized and uniformly distributed magnesium oxide particles.
- Hydrothermal method: In a high-temperature and high-pressure aqueous solution, magnesium oxide particles with a specific particle size distribution can be prepared by regulating the reaction time, temperature and pressure.
- Sol-gel method: This method forms a magnesium oxide precursor with a nano-scale particle size distribution through the polymerization and gelation process of the sol, and then obtains the final product through heat treatment. The particle size distribution can be controlled by regulating the concentration, pH value, reaction temperature and other conditions of the sol.
Controlling reaction conditions
- Reaction temperature: High temperature is conducive to accelerating the reaction rate, but it may also lead to increased particle size and uneven distribution. Therefore, it is necessary to select a suitable reaction temperature according to the specific reaction system.
- Reaction time: Too long a reaction time may lead to increased particle size and agglomeration, while too short a reaction time may not form a complete crystal structure. Therefore, the reaction time needs to be precisely controlled.
- Stirring intensity: Appropriate stirring is conducive to the uniform mixing and mass transfer process of the reactants, thereby controlling the particle size distribution. However, too strong stirring may destroy the formed crystal structure.
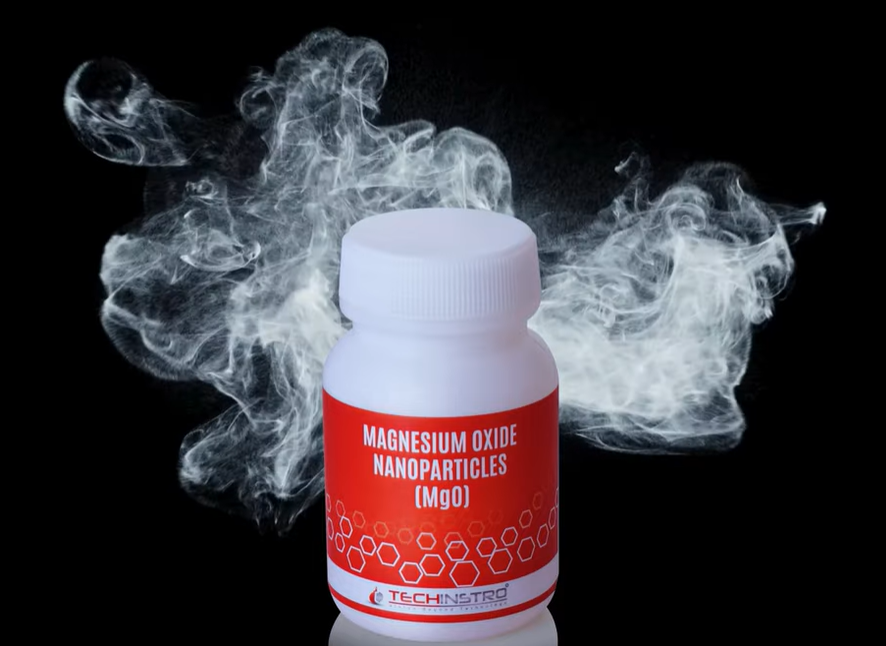
Post-treatment process
- Washing and centrifugation: The impurities and unreacted raw materials attached to the surface of magnesium oxide particles can be removed by washing and centrifugation, thereby purifying the product and improving the particle size distribution.
- Grinding and screening: For magnesium oxide particles with larger particle size, the particle size can be further refined and the particle size distribution can be adjusted by grinding and screening processes.
Control of specific surface area
Specific surface area is one of the important parameters for the adsorption performance and catalytic performance of magnesium oxide. The methods for controlling the specific surface area of magnesium oxide mainly include the following aspects:
Selecting a suitable preparation method
- As mentioned above, preparation methods such as sol-gel method, precipitation method and hydrothermal method can control the specific surface area of magnesium oxide by regulating the reaction conditions. Among them, the sol-gel method can usually obtain magnesium oxide products with a higher specific surface area.
Regulating pore size and pore structure
- By introducing templates, surfactants or controlling the growth conditions of crystals during the preparation process, the pore size and pore structure of magnesium oxide can be regulated, thereby increasing its specific surface area. For example, the use of template method to prepare mesoporous magnesium oxide can significantly increase the specific surface area.
Heat treatment process
- Appropriate heat treatment process can remove impurities and defects on the surface of magnesium oxide, optimize the crystal structure, and thus increase the specific surface area. However, excessively high heat treatment temperature may lead to crystal growth and pore collapse, thereby reducing the specific surface area.
Surface modification treatment
- By introducing specific functional groups or coating treatment on the surface of magnesium oxide, its surface properties can be improved and its specific surface area can be increased. For example, surface modification of magnesium oxide using silane coupling agent can significantly improve its dispersibility and specific surface area in aqueous solution.
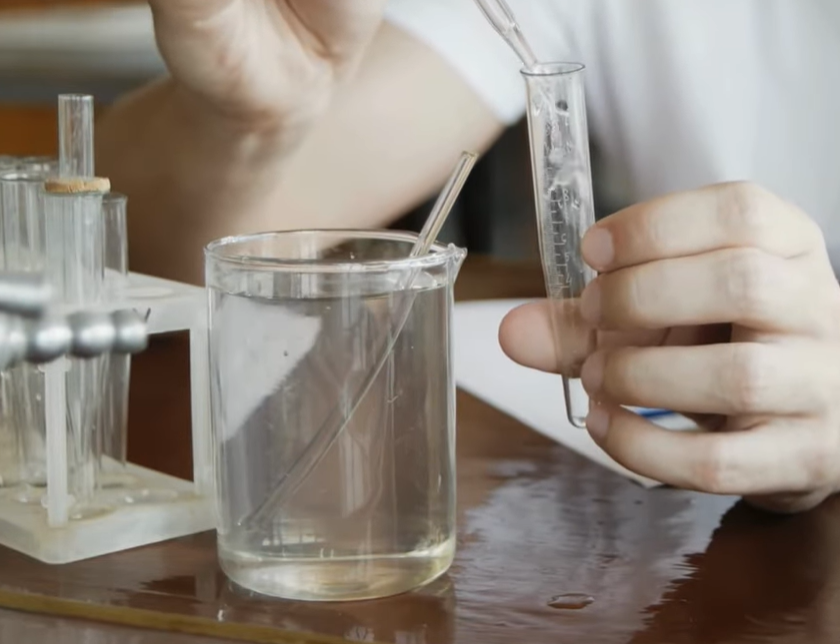
Comprehensive control strategy
In practical applications, it is often necessary to comprehensively consider the control strategy of particle size distribution and specific surface area. The following are some suggestions for comprehensive control strategies:
- Multi-step synthesis method: Combining the advantages of multiple preparation methods, a multi-step synthesis method is used to prepare magnesium oxide products with ideal particle size distribution and specific surface area. For example, a magnesium oxide precursor with a high specific surface area can be prepared by the sol-gel method, and then its particle size distribution and crystal structure can be further controlled by the hydrothermal method or heat treatment process.
- In-situ characterization and feedback control: In the preparation process, in-situ characterization technology (such as X-ray diffraction, transmission electron microscopy, etc.) is introduced to monitor the particle size distribution and specific surface area changes of magnesium oxide in real time, and the preparation process parameters are adjusted according to the feedback results to achieve precise control.
- Multidisciplinary cross-collaboration: Since the control of particle size distribution and specific surface area involves knowledge and technical means in multiple disciplines, it is necessary to strengthen multidisciplinary cross-collaboration and jointly promote the in-depth development of related research.
Summary
Controlling the particle size distribution and specific surface area of magnesium oxide is a complex and delicate process, which requires comprehensive consideration of multiple factors such as raw material selection, preparation process, reaction conditions, and post-treatment process.
Through continuous optimization and innovation of preparation methods and technical means, magnesium oxide products with ideal particle size distribution and specific surface area can be prepared to meet the application needs of different fields.
How to contact electronic component manufacturers?
E-components.globalbestshopping.com is a Chinese electronic component design and manufacturing manufacturer. We focus on electronic component OEM and ODM services. At the same time, we provide electronic component sales and wholesale services for global users.
We provide you with a BOM list for electronic component procurement. If you need to purchase electronic components or need to advertise on the electronic component website, you can contact us. Our electronic component website is open to all manufacturers. You can place advertisements as you want and get more accurate customers.
FAQs
The reasons for uneven particle size distribution may include uneven raw material concentration, improper selection of precipitant, and inaccurate control of reaction conditions. In addition, factors such as stirring speed and temperature fluctuations during the preparation process may also lead to uneven particle size distribution.
The methods for increasing the specific surface area of magnesium oxide mainly include reducing the particle size, regulating the pore structure, and selecting appropriate heat treatment conditions. By optimizing these preparation parameters, magnesium oxide materials with high specific surface area can be obtained.
The reasons for negative values in the specific surface area test may include problems with the sample itself (such as the adsorbate not being adsorbed), too little sample added in the test, irregular degassing temperature and duration, etc. These problems should be avoided during the test to ensure the accuracy of the test results.