The chemical element composition of the capacitor mainly includes metal electrodes and electrolytes. Metal electrodes usually use metal materials with good electrical conductivity such as aluminum and tantalum, while electrolytes choose different types of dielectric materials according to different application requirements.
The working principle of capacitors is mainly based on the storage and release of electric charge. When a voltage is applied between the two plates of the capacitor, the charge will be distributed on the two electrode plates of the capacitor, forming an electric field. When the voltage is removed, the charges are redistributed, creating a reverse electric field. This process is the charging and discharging process of the capacitor.
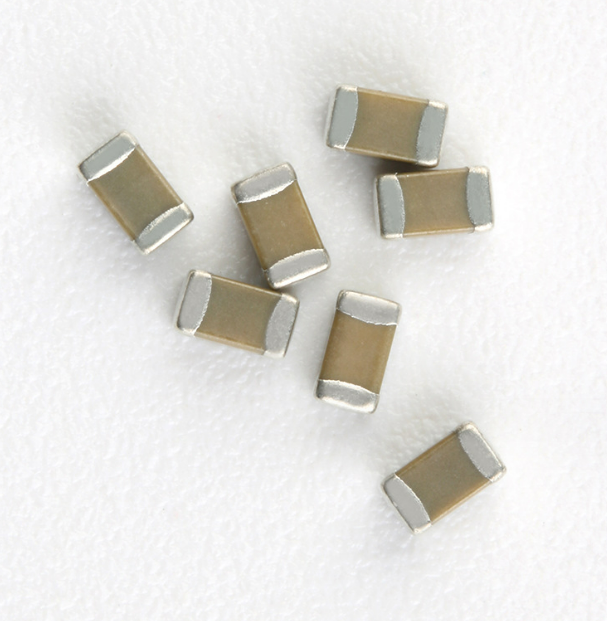
During the charging and discharging process of the capacitor, electrical energy will be converted into other forms of energy, such as thermal energy or mechanical energy. Therefore, capacitors play a role in storing and transmitting energy in circuits and are widely used in various electronic devices.
What are the chemical elements of a capacitor?
The chemical element composition of the capacitor mainly includes metal electrode materials and electrolyte materials.
- Metal electrode material: Metals with high conductivity are usually selected, such as aluminum, tantalum, etc. These metals are treated with special chemicals to form extremely thin metal foils, thereby increasing the surface area of the electrode and improving the energy storage density of the capacitor.
- Electrolyte material: This is another important component in the capacitor. Its function is to form a conductive path between the two electrodes. Depending on the type of electrolyte, capacitors can be divided into many types, such as electrolytic capacitors, ceramic capacitors, plastic film capacitors, etc. The electrolyte can be liquid, solid or gel, and its chemical composition determines the performance parameters of the capacitor, such as capacitance, operating voltage, temperature coefficient, etc.
In addition, packaging materials are also an important part of capacitors. They are mostly plastics or ceramics with good insulation and mechanical strength. The choice of packaging material also affects the performance and service life of the capacitor.
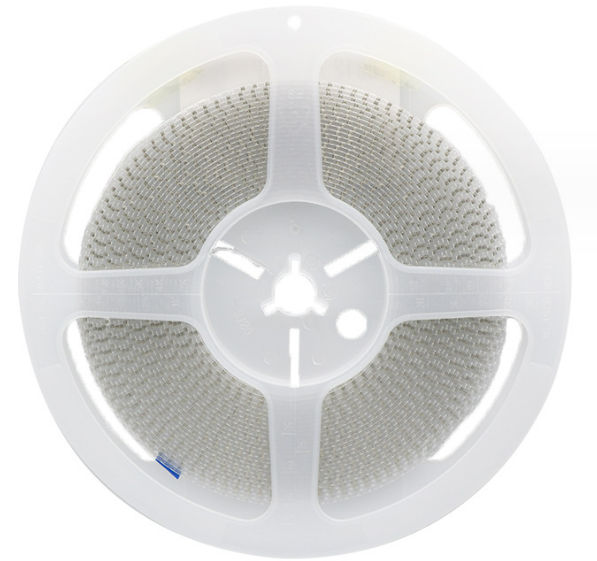
Analysis of the chemical element composition and working principle of capacitors
introduction
Capacitor, as a basic component in electronic circuits, has the characteristics of storing electrical energy and regulating the voltage and current in the circuit. This article will deeply analyze the nature of capacitors from the aspects of chemical element composition and working principle, in order to help readers better understand the basic knowledge of this electronic component.
The chemical composition of capacitors
Electrode materials
The main component of a capacitor is the electrode, whose material is usually made of highly conductive metals, such as aluminum, tantalum, etc. These metals are treated with special chemicals to form extremely thin metal foils, thereby increasing the surface area of the electrode and improving the energy storage density of the capacitor.
Electrolytes
The electrolyte is another important component in a capacitor, and its role is to form a conductive path between the two electrodes. Depending on the type of electrolyte, capacitors can be divided into many types, such as electrolytic capacitors, ceramic capacitors, plastic film capacitors, etc. The electrolyte can be liquid, solid or gel, and its chemical composition determines the performance parameters of the capacitor, such as capacitance, operating voltage, temperature coefficient, etc.
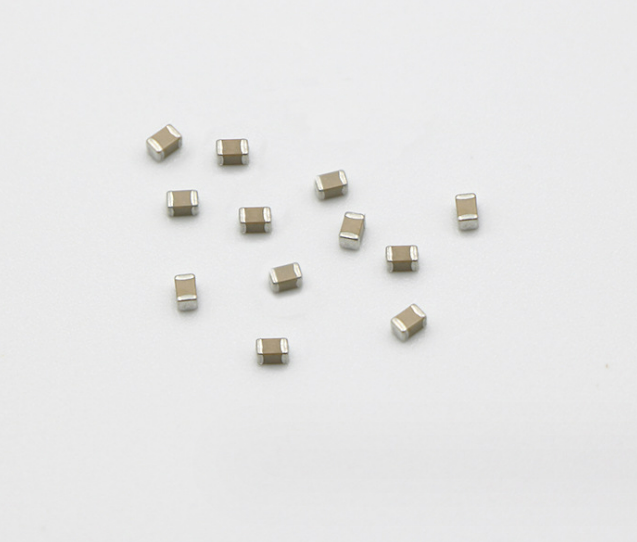
Packaging materials
In order to protect the internal structure of the capacitor and facilitate its use, packaging materials are usually added to the outside. The packaging materials are mostly plastic or ceramic, which have good insulation and mechanical strength. The choice of packaging material also affects the performance and service life of the capacitor.
Analysis of the working principle of capacitors
Energy storage principle of capacitor
When a voltage is applied across the capacitor, the charges on the electrodes will move into the electrolyte under the action of the electric field force, forming a charge layer opposite to the applied voltage. This process allows the capacitor to store electrical energy. Capacitance is an important parameter that measures the ability of a capacitor to store electrical energy, and its unit is usually Farad (F). The size of the capacitance depends on factors such as the conductivity of the electrode material, the composition of the electrolyte, and the distance between the electrodes.
The charging and discharging process of capacitor
When the applied voltage changes, the capacitor will undergo a charge and discharge process. During the charging process, the applied voltage gradually increases, causing the charge on the electrode to continue to increase until an equilibrium state is reached. At this time, the voltage across the capacitor is equal to the applied voltage, and the energy stored in the capacitor reaches its maximum value. During the discharge process, the applied voltage gradually decreases or disappears, and the charge on the electrode is gradually released through the load in the circuit until the voltage across the capacitor drops to zero. This process realizes the conversion and transmission of electrical energy.
Frequency characteristics of capacitor
Due to the energy storage and discharge functions of capacitors in circuits, they have specific frequency characteristics. For high-frequency signals, the capacitor has a small impedance and can be used as a bypass component in the circuit; while for low-frequency signals, the capacitor has a large impedance and can be used as a DC-blocking component in the circuit. This frequency characteristic makes capacitors widely used in electronic circuits.
Conclusion and Outlook
This article provides an in-depth analysis of capacitors from two aspects: chemical element composition and working principle. By understanding the composition materials and energy storage principles of capacitors, we can better understand their role and application in electronic circuits. In the future, with the continuous advancement of science and technology and the emergence of new materials and new processes, the performance and types of capacitors will become more diverse. This will bring more choices and possibilities in the design and manufacturing of electronic circuits.
Is there any relationship between capacitor packaging material and temperature?
There is a certain relationship between capacitor packaging materials and temperature.
First, the choice of packaging material will affect the temperature resistance of the capacitor. Different packaging materials have different thermal expansion coefficients and thermal conductivity properties, which will affect the temperature range and service life of the capacitor. For example, some capacitors encapsulated in metal shells have good high temperature resistance, while some capacitors encapsulated in plastic shells may be affected by high temperatures and cause deformation or aging.
Secondly, the thermal conductivity of the packaging material will also affect the temperature stability of the capacitor. If the thermal conductivity of the packaging material is poor, the heat generated by the capacitor during operation may not be transferred out in time, causing the internal temperature of the capacitor to rise, thereby affecting its performance and service life.
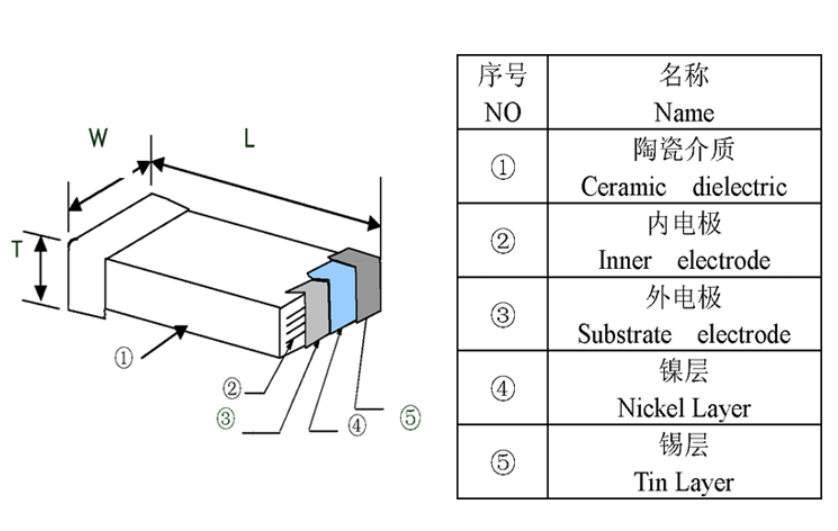
In addition, the insulation properties of the packaging material will also affect the temperature resistance of the capacitor. If the insulation performance of the packaging material is poor, the capacitor may be affected by the external environment during operation and cause problems such as leakage or short circuit, thus affecting its temperature resistance and service life.
To sum up, there is a certain relationship between capacitor packaging materials and temperature. Choosing the appropriate packaging material can ensure the temperature resistance and service life of the capacitor. At the same time, when using capacitors, you also need to pay attention to factors such as its working environment temperature and service life to avoid affecting its performance and service life due to too high or too low temperature.
What are the effects of capacitor packaging materials and packaging processes?
The packaging material and packaging process of the capacitor have an important impact on its performance and service life.
First, the choice of packaging materials affects the electrical properties, mechanical properties and environmental adaptability of the capacitor. For example, metal packaging materials have good thermal and electrical conductivity, which can effectively protect the internal structure of the capacitor and improve its electrical and mechanical properties. Plastic packaging materials have the advantages of low cost, light weight, and corrosion resistance, but their mechanical strength and electrical properties are relatively poor.
Secondly, the packaging process will also affect the performance and service life of the capacitor. Different packaging processes will lead to differences in the size, weight, electrical performance and mechanical properties of capacitors. For example, the leaded packaging process has higher production efficiency and lower cost, but the capacitor is larger and may have larger parasitic inductance problems in high-frequency circuits. The chip packaging process can make the capacitor smaller, lighter, and have smaller parasitic inductance, making it more suitable for use in high-frequency circuits.
In addition, the packaging process also affects the reliability of the capacitor. For example, during the welding process, if the welding is poor or the welding time is too long, it may cause damage to the internal structure of the capacitor or reduce its performance. At the same time, during the assembly process, if the assembly is improper or inappropriate fasteners are used, the capacitor may also become loose or damaged.
To sum up, the packaging materials and packaging processes of capacitors have an important impact on their performance and service life. When selecting packaging materials and packaging processes, comprehensive considerations need to be made based on specific application scenarios and needs to ensure the optimal performance and service life of the capacitor.
Is there any relationship between capacitor packaging material and frequency?
There is a certain relationship between capacitor packaging materials and frequency.
First, different packaging materials have different electrical performance parameters such as dielectric constant and loss tangent value. These parameters will affect the equivalent series resistance (ESR) and equivalent series inductance (ESL) of the capacitor, thereby affecting the frequency response characteristics of the capacitor.
Secondly, the packaging process will also affect the frequency response characteristics of the capacitor. For example, the parasitic inductance of the lead-type packaging process is larger, while the parasitic inductance of the patch-type packaging process is smaller. These parasitic inductances will affect the frequency response characteristics of the capacitor, causing its performance to degrade in high-frequency circuits.
In addition, packaging materials and processes can also affect the stability of the capacitor. For example, some metal-cased capacitors may be affected by oxidation or corrosion in high-temperature environments, resulting in a decrease in their electrical performance. Some capacitors encapsulated in plastic shells may be affected by temperature changes and cause problems such as aging or deformation.
To sum up, there is a certain relationship between capacitor packaging materials and frequency. When selecting a capacitor, comprehensive considerations need to be made based on specific application scenarios and needs to ensure that the frequency response characteristics and stability of the capacitor are optimal.
Top 10 capacitor manufacturers and suppliers in China
Fujian Torch Electronic Technology Co., Ltd.
Torch Electronics is an enterprise focusing on the R&D, manufacturing, sales and service of capacitors. The company was established on December 20, 2007 and is headquartered in Fuzhou City, Fujian Province.
Torch Electronics’ capacitor products are widely used in aviation, aerospace, shipbuilding, communications, electric power, rail transportation, new energy and other fields. In addition, the company also has 7 wholly-owned subsidiaries and 2 holding subsidiaries, mainly engaged in capacitor R&D, manufacturing, sales and service.
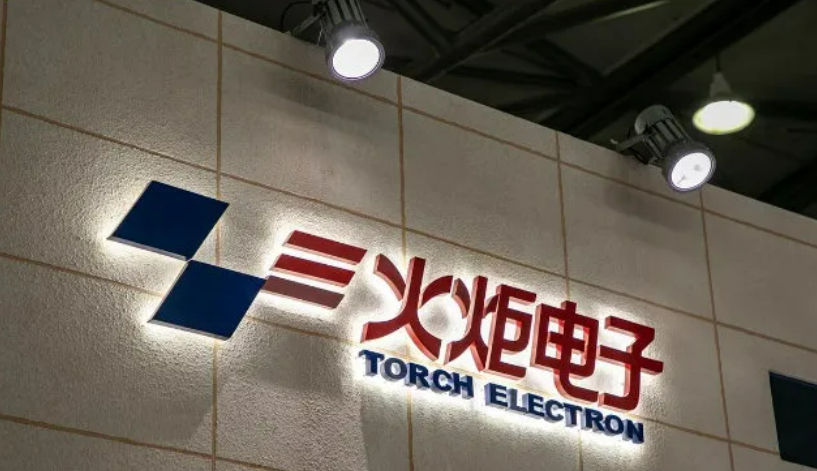
In terms of technology, Torch Electronics has advanced technology and R&D capabilities, and its products are popular for their leading technology and reliable quality. In addition, the company also focuses on marketing concepts and service follow-up, and is committed to pursuing multi-win situations to meet customer needs.
Nantong Jianghai Capacitor Co., Ltd.
Nantong Jianghai Capacitor Co., Ltd. is an enterprise mainly engaged in the production, sales and service of capacitors, their materials and accessories. The company was founded in 1958 and began specializing in the production of aluminum electrolytic capacitors in 1970. The company currently occupies an area of 120,000M2, with a building area of 60,000M2, more than 1,200 employees, and five joint venture affiliated companies. It is a national high-tech enterprise and a key enterprise of the National Torch Plan-Tongzhou Electronic Components and Materials Industry Base.
In terms of products, the aluminum electrolytic capacitors of Nantong Jianghai Capacitor Co., Ltd. have excellent self-healing characteristics, high reliability, and high cost performance. They are widely used in industrial controllers, various power supplies, new energy, white goods, military industry and other fields. . In addition, the company’s metallized film capacitors have the characteristics of small equivalent series resistance, large ripple current tolerance, self-healing, good safety features, and long service life. They are widely used in power electronics, new energy, and military industries. and other fields.
In terms of honors, Nantong Jianghai Capacitor Co., Ltd. has been selected as one of the top 100 enterprises in China’s electronic components industry selected by the China Electronic Components Industry Association for many consecutive years. In addition, the company has ranked first in the domestic aluminum electrolytic capacitor industry in terms of sales revenue since 1993. In September 2010, it was listed on the SME Board of the Shenzhen Stock Exchange.
Nantong Jianghai Capacitor Co., Ltd. has rich experience and good performance in the field of capacitors, and is a capacitor supplier worth considering.
Aihua
Aihua Capacitor Co., Ltd. is a company specializing in the production and sales of aluminum electrolytic capacitors. It has a complete industrial chain from corrosion foil, chemical foil to aluminum electrolytic capacitors, and independently develops a capacitor quality management software system. The company is committed to providing high-quality aluminum electrolytic capacitors to the world. After years of development, the company continues to improve and develop new products, and its independent innovation capabilities continue to increase.
Fara Electronics
Xiamen Fara Electronics Co., Ltd. is a listed company specializing in the development and production of film capacitors and metallized films for film capacitors. The company has a strong R&D center and an experienced technical service team, with an annual output of 4.5 billion film capacitors and 2,500 tons of metallized films. The company’s products are widely used in communications, home appliances, lighting, automobiles, industrial control and other fields, and have passed ISO9001 quality system certification, ISO14001 environmental management system certification, and OHSAS18001 occupational health and safety management system certification.
Shenzhen Jinpenghui Technology Co., Ltd.
Shenzhen Jinpenghui Technology Co., Ltd. is a high-tech company integrating R&D and sales, located in Shenzhen, Guangdong Province. The company mainly sells Zhaoqing emerald electrolytic capacitors, emerald capacitors, BERYL electrolytic capacitors, KFSON capacitors, Kangfusong electrolytic capacitors, solid electrolytic capacitors, solid capacitors and other products. These products are widely used in LED light driving power supplies, electronic energy-saving lamps and ballasts, stage amplifiers, vehicle electronic equipment, computer motherboards, security products, inverters, network communications, medical equipment power supplies, UPS and other fields.
Fenghua Hi-Tech
Guangdong Fenghua High-tech Co., Ltd. is a company specializing in the development, design, manufacturing and sales of electronic components and materials, and integrated circuits. Its products are widely used in communications, consumer electronics, computers, automotive electronics, new energy and other fields.
One of the largest manufacturers of passive electronic components in China, its main products include capacitors, resistors, inductors, etc.
Beijing Yuanliu Hongyuan Electronic Technology Co., Ltd.
Beijing Yuanliu Hongyuan Electronic Technology Co., Ltd. is a high-tech enterprise of electronic components mainly engaged in the development, production and operation of multi-layer (chip) ceramic capacitors. The company is headquartered in Fengtai Science and Technology Park, Zhongguancun, Beijing, and its production base is built in Jinnan Shuanggang Economic Development Zone, Tianjin.
For many years, the company has been committed to the R&D and production of multilayer ceramic capacitors. It has a complete multilayer ceramic capacitor production line and has routine experiments, destructive physical analysis (DPA) and material (chip) electrical and process performance certification. Three key laboratories and a number of domestic and foreign advanced equipment and facilities provide a strong guarantee for ensuring product quality.
Tongfeng Electronics
Anhui Tongfeng Electronics Co., Ltd. (hereinafter referred to as: Tongfeng Electronics) is a company engaged in the research, development, production and sales of film capacitors and film materials. It has advantages in technology and research and development, integrated industrial chain, and brand.
Three-Circle (Group)
Chaozhou Three-Circle (Group) Co., Ltd. was established in 1970 and listed on the Shenzhen Stock Exchange in 2014 (stock code: 300408). It is a company dedicated to the research and development, production and sales of electronic basic materials, electronic components, communication devices and other products. comprehensive enterprise. The company’s products cover many application fields such as optical communications, electronics, electrical engineering, machinery, energy conservation and environmental protection, new energy and fashion. Among them, the production and sales of optical fiber connector ceramic ferrules, alumina ceramic substrates, and ceramic substrates for resistors rank among the top in the world. The company has been rated as a national technology enterprise and a single champion demonstration enterprise in China’s manufacturing industry. It has been ranked among the top ten of China’s top 100 electronic components for many consecutive years.
Yageo
Yageo Co., Ltd. is the world’s leading brand of passive components. Founded in 1977, it is Taiwan’s first listed electronic components company. Yageo Electronics (Suzhou) Co., Ltd. is a wholly-owned subsidiary of Yageo Co., Ltd. in China. It was registered and established in March 2001. The company’s business scope includes the production of electronic components, new electronic components, new instrument circuit boards, etc.
In addition, Yageo Co., Ltd. has also launched products such as tantalum nitride films and high-precision resistors with anti-humidity and anti-sulfur properties.
Yageo Co., Ltd. was founded in 1977. It is the largest supplier of passive components in Taiwan and the largest professional capacitor manufacturer in the world. It is Taiwan’s first listed passive component and is an international enterprise with global production and sales bases.