Inductors are commonly used components in electronic circuits and have functions such as galvanic isolation, signal conditioning, and filtering.
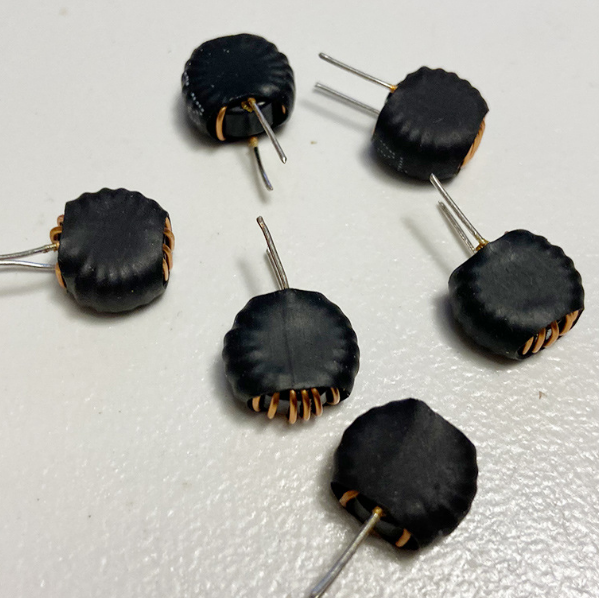
The performance of an inductor depends primarily on the properties of the materials from which it is made. Therefore, research on inductor manufacturing materials is an important direction for the development of inductor technology.
11 top notch inductor manufacturing materials list
Soft magnetic materials
The core material of the inductor mainly uses soft magnetic materials. Soft magnetic materials have large magnetic permeability and low hysteresis loss, which are important performance indicators of the inductor. Commonly used soft magnetic materials include ferrite, iron powder core, nanocrystalline alloy, etc.
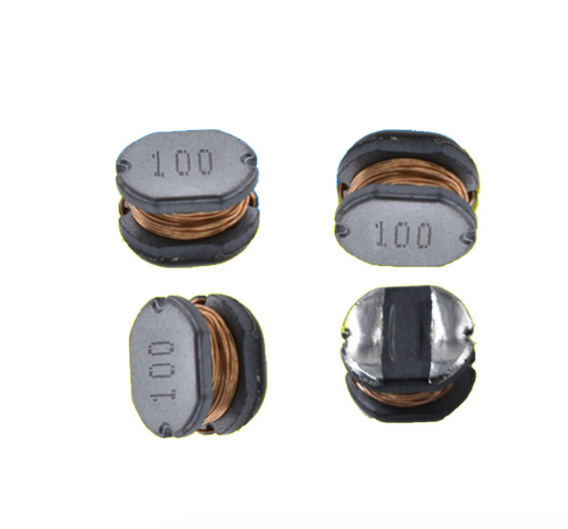
ferrite
Ferrite is currently the most widely used soft magnetic material with good magnetic properties, mechanical properties and corrosion resistance. Ferrite inductors have the advantages of small size, light weight, and low cost, and are mainly used in low-frequency and medium-frequency circuits.
Iron powder core
The iron powder core is pressed by iron powder and binder and has high magnetic permeability and low hysteresis loss. Iron powder core inductors have high power density and are mainly used in high-frequency and high-power circuits.
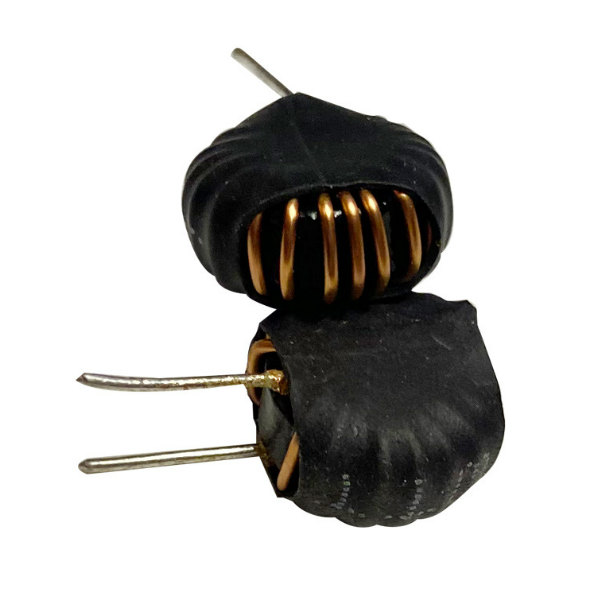
Nanocrystalline alloy
Nanocrystalline alloy is a new type of soft magnetic material developed in recent years, with ultra-high magnetic permeability and ultra-low hysteresis loss. Nanocrystalline alloy inductors have excellent high-frequency performance and are mainly used in high-frequency and high-speed circuits.
Insulation Materials
The coil of the inductor is wound on the magnetic core, and insulating materials need to be used to isolate the coil from the magnetic core to prevent short circuits. Commonly used insulation materials include enameled wire, polyester film, ceramics, etc.
Enameled wire
Enameled wire is a commonly used insulating material for inductor coils. It is made of copper wire or aluminum wire wrapped with insulating paint. Enameled wire has good electrical conductivity, insulation and corrosion resistance.
Polyester film
Polyester film is an ideal insulating material for high-frequency applications of inductor coils, with good dielectric strength, dielectric loss and high temperature resistance.
ceramics
Ceramic is a material with high dielectric constant, good insulation and high temperature resistance. Ceramic inductors have the advantages of small size, light weight, and high temperature resistance, and are mainly used in high-frequency and high-temperature circuits.
Packaging materials
Inductors need to be packaged to protect them from the outside environment. Commonly used packaging materials include plastic, metal, etc.
plastic
Plastic is a low-cost, easy-to-process packaging material mainly used in low-cost, small inductors.
Metal
Metal has good thermal conductivity and corrosion resistance, and is mainly used in high-power, high-frequency inductors.
Manufacturing process of inductor
The manufacturing process of inductors mainly includes magnetic core manufacturing, coil winding and packaging.
Core manufacturing
Magnetic core manufacturing is the first step in inductor manufacturing, which mainly includes the sintering of ferrite cores, the pressing of iron powder cores, and the sintering of nanocrystalline alloy cores.
coil winding
Coil winding is a key step in inductor manufacturing, which mainly includes coil cutting, coil winding and coil fixing.
Inductor packaging
Packaging is the last step in inductor manufacturing, which mainly includes inductor assembly, inductor testing, and inductor packaging.
Inductor packaging technology refers to the process of assembling the core, coil and pins of an inductor together. The main packaging methods of inductors are as follows:
Chip inductor
Chip inductors are currently the most widely used inductor packaging method. The magnetic core and coil of the chip inductor are made of enameled wire. After the coil is wound on the magnetic core, the two ends of the coil are led out, and the pins are soldered to the printed circuit board. Chip inductors have the advantages of small size, light weight, and low cost, and are mainly used in low-frequency and medium-frequency circuits.
Multilayer inductor
A laminated inductor is an inductor package in which multiple magnetic cores and coils are laminated together. Multilayer inductors have high magnetic permeability and low hysteresis loss, and are mainly used in high-frequency and high-power circuits.
Metal package inductor
Metal package inductors are inductor packages that encapsulate the inductor’s core, coil and pins in a metal shell. Metal package inductors have good thermal conductivity and corrosion resistance and are mainly used in high-power and high-frequency circuits.
The development trends of inductor packaging technology mainly include the following aspects:
Develop towards miniaturization, lightweight and thinness
With the continuous development of electronic products, the requirements for the size, weight and thickness of inductors are getting higher and higher. The continuous development of inductor packaging technology provides the possibility to meet these requirements.
Developing towards high frequency and high power
As the frequency of electronic products continues to increase, the requirements for the high-frequency performance and power density of inductors are getting higher and higher. The continuous development of inductor packaging technology provides the possibility to meet these requirements.
Develop towards multi-function and intelligence
As the functions of electronic products continue to be enriched, the requirements for the versatility and intelligence of inductors are getting higher and higher.
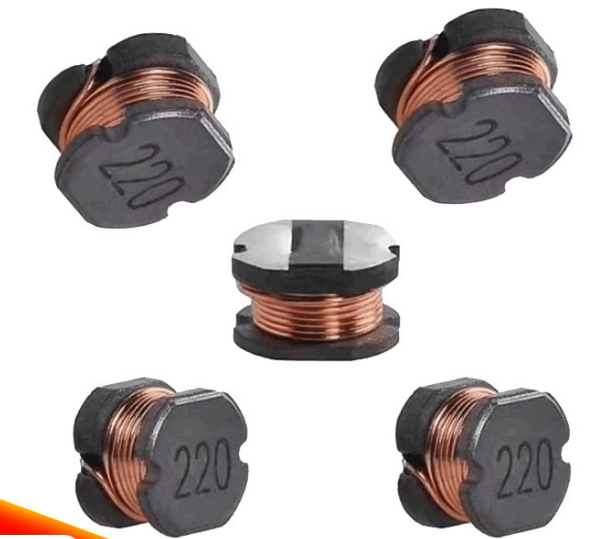
The continuous development of inductor packaging technology provides the possibility to meet these requirements.
Research trends in inductor manufacturing materials
Research on manufacturing materials for inductors mainly focuses on the following directions:
Improve the performance of soft magnetic materials
By improving the material composition, structure and processing technology of soft magnetic materials, the magnetic permeability, low hysteresis loss and high frequency performance of soft magnetic materials can be improved.
Develop new inductor materials
Develop inductor materials with special properties, such as high-frequency inductors, high-power inductors, high-temperature inductors, etc.
Improving inductor manufacturing efficiency
Develop advanced manufacturing processes to improve inductor manufacturing efficiency and cost-effectiveness.
Research on inductor manufacturing materials is an important direction for the development of inductor technology and will promote the progress of inductor technology.