The braking resistor is a kind of ripple resistor, which is mainly used in mechanical systems where the inverter controls the motor to stop quickly to help the motor convert the regenerated electric energy generated by the motor into heat energy.
The working principle of the braking resistor is based on Ohm’s law and Joule’s law. During the motor braking process, the braking resistor converts the energy generated by the motor into heat energy for heat dissipation and limits the inertia of the motor during motion.
When the motor starts braking, the motor will provide a certain current and voltage to the braking resistor. The braking resistor contains a series of metal materials, such as copper, iron, chromium, etc., all of which have a certain resistivity.
When current passes through the braking resistor, resistance loss will occur, that is, a large amount of heat will be generated inside the braking resistor, converting the energy generated by the motor into thermal energy. At the same time, by adjusting the resistance of the braking resistor, the braking time and braking torque of the motor can be controlled to meet the needs of different mechanical systems.
In addition, the braking resistor can also be used to absorb the overvoltage generated by the frequency converter to prevent the energy generated by the motor when decelerating or stopping from damaging the semiconductor devices inside the frequency converter. When the voltage in the DC circuit exceeds the allowable range, the braking resistor can absorb the excess energy and keep the DC voltage within the normal range, thereby protecting the inverter and motor.
In short, the braking resistor is an auxiliary component used for the inverter to control the motor. Its working principle is based on Ohm’s law and Joule’s law. It dissipates heat by converting the energy generated by the motor into heat energy and limits the inertia of the motor to achieve rapid speed of the motor. Stop and overvoltage protection of the frequency converter.
Common classification of braking resistors
Common braking resistors are classified as follows:
- Classification according to resistance characteristics: fixed resistor, adjustable resistor, special resistor (sensitive resistor). Among them, fixed resistors are resistors with fixed resistance, usually printed with color marking or direct marking; adjustable resistors are similar to those learned in junior high school physics, and the resistance value is changed by changing the length of the coil; special resistors include Varistor, negative temperature coefficient thermistor, etc.
- Classified by manufacturing materials: carbon film resistors, metal film resistors, wirewound resistors, non-inductive resistors, thin film resistors, chip resistors, etc. These resistors are widely used in different electronic devices, with their own characteristics and application scenarios.
- Classification by power: Power braking resistors are mainly used in high-power, high-current circuits and have high power dissipation capabilities. This kind of resistor is usually made of metal foil or metal strip, which has a large heat dissipation area and good heat dissipation performance. Precision braking resistor is a precision resistor device with high accuracy and stability. This kind of resistor is usually made of materials such as metal film, metal powder or metal oxide, and has a small temperature coefficient and good linear characteristics.
- Classification by cooling form: When the braking resistor consumes the excess regenerative energy of the train, it generates a large amount of heat energy that must be dissipated into the atmosphere. Therefore, if effective heat dissipation measures cannot be taken, the heat energy generated by the braking resistor will accumulate inside the braking resistor, which is enough to cause the braking resistor to burn out in a short period of time. According to the cooling mode, braking resistors can be divided into two types: forced ventilation cooling braking resistors and natural ventilation cooling braking resistors.
What are the characteristics of braking resistors?
The characteristics of braking resistors mainly include the following aspects:
- High efficiency: The resistance value and power capacity of the braking resistor are important parameters. Its design helps to quickly and effectively convert the regenerative energy of the motor into heat energy, thereby ensuring the stable operation of the motor system.
- Safety: The application of braking resistors can effectively protect the inverter and motor from frequent tripping due to overvoltage, shortened equipment life or high maintenance costs, damage to the motor and driver, and/or overheating.
- Reliability: The design of braking resistors usually uses high-quality materials and manufacturing processes, which have high reliability and stability.
- Durability: The resistance wire of the braking resistor has good high temperature resistance, can effectively resist aging and extend the service life.
- Environmental adaptability: Braking resistors usually have good weather resistance and vibration resistance, and can operate stably under harsh environmental conditions.
- Diversity: There are various types of braking resistors, including corrugated resistors and aluminum alloy resistors, which are suitable for different application scenarios and needs.
- Easy maintenance: The design of the braking resistor makes it easy to install, attach a heat sink and inspect, making it easy to maintain.
In short, braking resistors are widely used in various situations that require quick stopping or deceleration due to their high efficiency, safety, reliability, durability, environmental adaptability and diversity.
What material is the braking resistor made of?
Braking resistors are usually made of metallic materials such as copper and nichrome wire. Copper is a good conductive material with good electrical and thermal conductivity, while nickel-chromium alloy has high-temperature oxidation resistance. In addition, oxygen-free copper is often used as the joint material of the braking resistor during the production process to ensure the stability of the connection and the reliability of the resistance properties.
In addition, there are several other possible materials for braking resistors, including iron-based alloys, nickel alloys, copper alloys, metal oxides, etc. These materials have high resistivity and thermal conductivity, as well as good corrosion resistance and oxidation resistance.
In general, the material selection of the braking resistor needs to be determined according to the needs and environment of the actual application to ensure its normal operation and long service life.
Precautions for selecting brake electronics
When selecting a braking resistor, there are several key factors to consider:
- Resistance value: Select the appropriate resistance value according to the motor parameters and working condition requirements. The choice of resistance value will affect the braking effect and energy consumption.
- Power: The power of the braking resistor should be large enough to withstand the energy generated during regenerative braking of the motor. Choosing the right power can avoid resistor overheating and damage.
- Heat dissipation performance: The braking resistor will generate a lot of heat during operation, so its heat dissipation performance needs to be considered. Choosing a suitable heat dissipation solution can ensure the stable operation of the braking resistor.
- Environmental adaptability: The braking resistor should be able to operate stably under harsh environmental conditions, such as high temperature, low temperature, humidity, vibration, etc. Choosing a braking resistor suitable for the environmental conditions can extend its service life.
- Brand and quality: Choosing a well-known brand and high-quality braking resistor can ensure its reliability and stability. At the same time, ensure that the braking resistor purchased complies with relevant standards and specifications.
- Installation and additional heat sink: The mounting method and additional heat sink of the braking resistor will also affect its performance and life. When selecting a braking resistor, consider its size and manner of mounting and whether an additional heat sink is required.
- Cost: The cost of the braking resistor is also one of the factors that needs to be considered. On the premise of meeting performance requirements, products with high cost performance should be selected.
To sum up, when selecting a braking resistor, you need to pay attention to many aspects such as resistance, power, heat dissipation performance, environmental adaptability, brand and quality, installation and additional radiator, and cost. Taking these factors into consideration ensures the performance and stability of the braking resistor and extends its service life.
Why use braking resistor?
The reason for using a braking resistor is mainly to solve the problem of processing a large amount of regenerative energy generated by the motor during rapid stopping or deceleration. When a motor needs to stop or decelerate quickly during operation, the magnetic field in its rotor interacts with the magnetic field in the stator to produce braking torque.
At this time, the motor will generate a large amount of regenerative energy and feed it back to the power supply side. If measures are not taken to deal with this regenerated energy, damage to the power supply and motor will occur. The use of braking resistors can effectively absorb this regenerated energy, convert it into heat energy and dissipate it into the atmosphere, thereby protecting the power supply and motor.
Specifically, the braking resistor can ensure the safety and stability of the motor during rapid stopping or deceleration. When a motor loses power, its rotor will continue to rotate for a period of time due to inertia. At this time, if there is no external braking measure, the motor may continue to run, causing an accident. The braking resistor can provide the necessary braking torque to help the motor stop rotating quickly and ensure the safety of the equipment.
In addition, the braking resistor helps protect the frequency converter from regenerative energy from the motor. As the motor slows down, the friction between the mechanical parts becomes smaller and smaller, which causes the motor to rotate faster.
If this part of the regenerated electric energy is not consumed in time, it will directly act on the DC circuit part of the inverter. In the worst case, it will cause the inverter to report a fault, and in serious cases, it may damage the inverter.
The emergence of braking resistors solves this problem well and protects the frequency converter from the harm of the regenerated electric energy of the motor.
To sum up, the purpose of using a braking resistor is mainly to handle the large amount of regenerative energy generated by the motor during rapid stopping or deceleration, ensure the safety and stability of the equipment, and protect the inverter from damage.
What is the function of braking resistor?
The braking resistor plays an important role in the mechanical system. It is mainly used to consume the regenerative energy of the motor in the form of heat energy and help the motor convert the regenerative electrical energy generated by the rapid stop into heat energy.
In the mechanical system where the inverter controls the motor to stop quickly, due to inertia, the motor will generate a large amount of regenerated electric energy during the quick stop process. If this part of the regenerated electric energy is not consumed in time, it will directly act on the DC circuit part of the inverter.
In mild cases, it will cause the inverter to report a fault, and in severe cases, it will damage the inverter. The emergence of braking resistors solves this problem well and protects the frequency converter from the harm of the regenerated electric energy of the motor.
In addition, the braking resistor can directly convert the regenerated electric energy into thermal energy, so that the regenerated electric energy will not be fed back into the power supply network and will not cause fluctuations in the grid voltage, thereby ensuring the smooth operation of the power supply network.
In general, the role of the braking resistor is to protect the frequency converter and power network from the harm of the motor’s regenerated electric energy and ensure the smooth operation of the system.
Braking resistor for VFD calculation
The braking resistor used in VFD (Variable Frequency Drive) calculations is mainly used to convert the regenerative energy generated by the motor into heat energy and consume it when the motor stops or decelerates quickly, so as to maintain the voltage on the DC bus within a normal value range.
The selection of braking resistor mainly depends on the rated power, rated current, rated voltage, speed and other parameters of the motor. When calculating the resistance of the braking resistor, you need to first calculate the back electromotive force of the motor and the required braking current, and then select the appropriate braking resistor based on the voltage and power of the braking unit.
In addition, the power and heat dissipation performance of the braking resistor also need to be considered. The power of the braking resistor should be large enough to withstand the energy generated during regenerative braking of the motor, and it needs to have sufficient heat dissipation performance to prevent the resistor from being damaged by overheating.
To sum up, the purpose of using braking resistors in VFD calculations is to achieve fast stopping and stable control of the motor, and the selection of the braking resistor needs to be determined based on the parameters of the motor and actual working conditions.
What is VFD calculation
VFD calculation refers to the control algorithm of Variable Frequency Drive (frequency converter). The frequency converter is a power electronic device used to change the operating power frequency of the motor, thereby changing the motor’s speed and power. The core of VFD calculation is to realize the speed and torque control of the motor to achieve the required operating status and performance.
VFD calculation needs to take into account factors such as motor parameters, working status, control requirements, and system working environment. During the calculation process, it is usually necessary to collect the current, voltage, speed and other signals of the motor, and perform corresponding processing and calculation according to the control algorithm. By adjusting the input power frequency of the motor, precise control of motor speed and torque can be achieved to meet a variety of application requirements.
VFD calculation involves a variety of control algorithms and technologies, including PID control, fuzzy control, neural network, etc. Among them, PID control is one of the most commonly used control algorithms. It achieves high-precision control of motor speed and torque through the adjustment of proportion, integral and differential. In practical applications, it is necessary to select an appropriate control algorithm according to specific application scenarios and requirements, and optimize and adjust it to achieve the best control effect.
Why braking resistor used in VFD
The reasons why frequency converters use braking resistors are as follows:
- In the variable frequency speed control system, the motor’s speed reduction and shutdown are achieved by gradually reducing the frequency. At the moment when the frequency decreases, the synchronous speed of the motor decreases, but due to mechanical inertia, the rotor speed of the motor does not change. When the synchronous speed is smaller than the rotor speed, the phase of the rotor current changes almost 180 degrees, and the motor changes from the electric state to the power generation state.
- At the same time, the torque on the motor shaft turns into braking torque, causing the motor speed to drop rapidly, and the motor is in a regenerative braking state. The electric energy regenerated by the motor is fed back to the DC circuit after full-wave rectification by the freewheeling diode. Since the electric energy of the DC circuit cannot be fed back to the grid through the rectifier bridge, it is absorbed only by the capacitance of the inverter itself. Although other parts can consume electric energy, the capacitor still has a short-term charge accumulation, forming a “pump voltage”, causing the DC voltage to rise. high. Excessive DC voltage will damage various components.
- In systems with relatively large mechanical inertia, braking resistors need to be used, such as elevators, CNC machine tools, hoists, etc. Because the braking resistor or braking unit + braking resistor can consume the energy generated by the motor turning into a generator, preventing this energy from damaging the inverter module of the frequency converter.
In summary, the role of the braking resistor in the inverter is to consume the electric energy generated during regenerative braking, maintain the voltage on the DC bus at a normal value, and prevent damage to various components.
How should the braking resistor be configured on the inverter?
The configuration of the braking resistor on the frequency converter mainly includes the following steps:
- Determine the resistance and power of the braking resistor. Select the appropriate braking resistor resistance and power based on parameters such as the motor’s rated current, braking time and motor’s rated voltage.
- Select a suitable braking unit. The braking unit is a device used to control the connection and disconnection of the braking resistor. The appropriate braking unit can be selected according to the power of the motor and the resistance of the braking resistor.
- Connect the braking resistor to the output side of the inverter and connect it to the motor. Make sure the connecting wire is thick enough to reduce line voltage drop.
- Adjust the parameters of the inverter. According to the actual situation, the parameters of the frequency converter need to be adjusted, including the connection time of the braking resistor, the resistance of the braking resistor, braking torque and other parameters, to ensure the normal operation of the system.
- Test the braking effect of the system. After the configuration is completed, the braking effect of the system needs to be tested to ensure that the braking resistor can work properly and effectively consume the regenerative energy of the motor.
To sum up, the configuration of the braking resistor on the inverter needs to be comprehensively considered based on the actual situation, including the parameters of the motor, the parameters of the braking resistor and the parameters of the inverter, etc. At the same time, it is necessary to select a suitable braking unit and ensure that the connecting wire is thick enough. After the configuration is completed, testing is required to ensure the normal operation of the system.
How to determine the resistance value of the braking resistor?
The resistance of the braking resistor depends on many factors, including the rated current of the motor, the braking time and the rated voltage of the motor.
Generally, the resistance of the braking resistor should be 2-3 times the rated current of the motor. If faster braking time is required, a lower resistance value can be selected and vice versa. At the same time, the rated voltage and frequency of the motor need to be considered to ensure that the selected resistor will work properly.
In addition, the power of the braking resistor also needs to be considered. The power of the braking resistor should be 1.5-2 times the rated power of the motor. If faster braking times are required, higher power can be selected and vice versa. At the same time, the temperature rise of the braking resistor also needs to be considered to ensure that it does not overheat and be damaged.
In addition, the type of braking resistor also needs to be determined. Braking resistors can be divided into two types: resistive and capacitive. Resistive braking resistors can provide stable braking effects, but consume more power; capacitive braking resistors can provide higher efficiency and lower power loss, but require more complex control circuits.
To sum up, the resistance value of the braking resistor needs to be selected according to the actual situation to achieve the best braking effect.
Is there any relationship between the resistance value of the braking resistor and the power?
There is a close relationship between the resistance value of the braking resistor and the power. When the power of the braking resistor is constant, the greater the resistance value, the smaller the current, and the heat dissipation capacity of the braking resistor will be reduced accordingly.
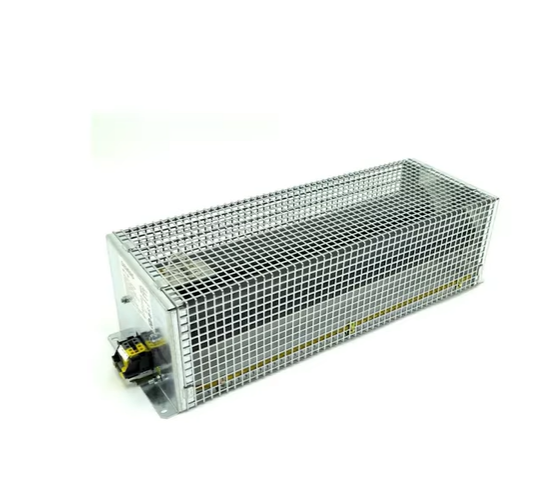
Therefore, when selecting a braking resistor, its resistance value and power need to be considered comprehensively to ensure that the braking resistor can work properly and absorb the energy generated by the motor.
At the same time, the heat dissipation capacity and reliability of the braking resistor also need to be considered to ensure that it can work stably for a long time. To sum up, the resistance value of the braking resistor is related to the power.
Braking resistor circuit diagram
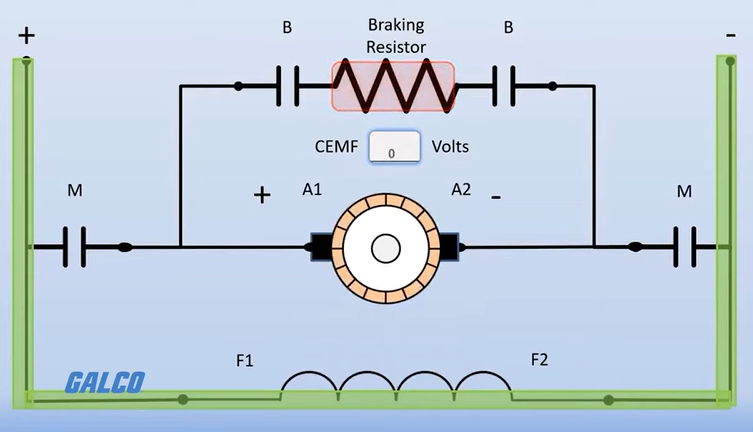
Braking resistor usage example
Application areas of braking resistors
The application fields of braking resistors are very wide, including but not limited to the following aspects:
- Elevator industry: Elevators generate a large amount of regenerated energy during their ascent or descent. In order to prevent this energy from causing harm to the elevator equipment, the braking resistor can be used to consume this energy and keep the elevator running stably.
- Rail transit industry: In subway or light rail vehicles, the motor generates a large amount of regenerative energy during braking. Braking resistors absorb this energy and prevent damage to the vehicle’s electrical system.
- Wind power industry: During the operation of wind turbines, especially when the wind speed is unstable, a large amount of regenerated energy will be generated. Braking resistors can be used to absorb this energy and protect wind turbine equipment.
- Industrial automation industry: In industrial automation production lines, motors will generate a large amount of regenerative energy when they stop or decelerate quickly. Braking resistors can be used to absorb this energy and protect the motor and the entire production line equipment.
- Ship industry: The ship’s propulsion motor generates a large amount of regenerative energy when decelerating or braking. Braking resistors can be used to absorb this energy and protect the ship’s electrical system.
- Electric vehicle industry: The motor of an electric vehicle generates a large amount of regenerative energy when stopping or decelerating quickly. Braking resistors can be used to absorb this energy, extending electric vehicle battery life and improving driving efficiency.
In short, braking resistors are used in many fields, especially in situations where quick stopping or deceleration is required, where they can play an important role.
What is Brake Resistor Calculator
The Braking Resistor Calculator is a tool for calculating the value of a braking resistor. By inputting the parameters of the motor, such as rated power, rated voltage, rated current and speed, etc., as well as the required control requirements, such as braking time, braking torque, etc., the braking resistor calculator can calculate the required braking resistor. resistance and power.
The braking resistor calculator can help engineers and operators better select and use braking resistors when designing and using frequency converters to ensure fast, stable and safe stopping or deceleration of the motor. By using a braking resistor calculator, you can avoid equipment damage or safety incidents caused by improper selection of a braking resistor.
Comparison of advantages and disadvantages of braking resistors
The advantages and disadvantages of braking resistors are as follows:
advantage:
- Simple structure, reliable operation and stable operation.
- It can quickly absorb the regenerative energy of the motor and convert it into heat energy for release, thereby avoiding damage to the inverter.
- It can effectively avoid main power overvoltage caused by motor regenerative energy and ensure the smooth operation of the power network.
- No special maintenance is required, reducing operating costs.
disadvantages:
- The size of the resistance value is related to the rated current of the motor, braking time and rated voltage of the motor, etc. It needs to be selected according to the actual situation, otherwise problems such as poor braking effect or overheating of the braking resistor may occur.
- The power of the braking resistor is relatively large, so you need to choose a high-power resistor, otherwise problems such as overheating or even burning of the resistor may occur.
- The braking resistor is large in size, takes up a certain amount of space, and weighs a lot, which will increase the burden on the system.
- The braking resistor will generate a certain amount of heat, and a suitable heat dissipation method needs to be selected, otherwise the working effect and life of the braking resistor will be affected.
To sum up, the braking resistor has the advantages of simple structure, reliable operation and stable operation. However, in practical applications, attention needs to be paid to selecting the appropriate resistance value, power and heat dissipation method to ensure its normal operation and extend its service life.
The difference between braking unit and braking resistor
Although both braking units and braking resistors are used to realize the braking function of motor control, there are some differences:
- The rated voltage, rated current and rated power of the braking resistor of the braking unit are determined and cannot be changed. The braking power will change due to the load, so the braking power of the braking unit is required to be equal to the braking rate of the load to ensure the stability of the DC voltage.
- The braking resistor is a resistor, which is mainly used to consume the regenerative energy of the motor as heat energy. The braking unit contains a braking resistor, a power supply, a DC voltage detection circuit, a drive and switching circuit composed of IGBT, and an energy consumption circuit composed of a braking resistor.
- The braking unit can be understood as a modular circuit structure, which has the function of turning the braking resistor on and off, and also includes power tubes, voltage sampling and comparison circuits and drive circuits.
- Braking units can be divided into two types: built-in type and external type. The former is suitable for low-power general-purpose inverters, and the latter is suitable for high-power inverters or working conditions with special requirements for braking.
To sum up, the braking unit is a comprehensive circuit structure that includes a braking resistor and other related circuits, and the braking resistor is just a resistive element used to consume regenerative energy. In practical applications, the appropriate braking unit and braking resistor can be selected as needed to meet the control requirements.
What will happen if the inverter is not connected to the braking resistor?
Not connecting the braking resistor to the frequency converter may cause some problems.
First of all, if the inverter is not connected to a braking resistor during operation, the regenerative energy of the motor cannot be effectively consumed, which will cause the motor to overheat, directly affecting the service life and reliability of the equipment.
Secondly, if the inverter is not connected to a braking resistor, when the load inertia is relatively large and the downtime is short, the motor may become a generator during the parking process, generating electric energy and directly applying it to the inverter module of the inverter. on, causing damage to the inverter module.
In addition, if the braking resistor is not connected, the electric energy generated by the motor when generating power cannot be consumed by the braking resistor, and will be fed back to the DC bus of the inverter, causing the DC bus voltage to increase until an overvoltage fault occurs.
To sum up, not connecting the braking resistor to the inverter may cause problems such as motor overheating, damage to the inverter module, and overvoltage faults. Therefore, in order to ensure the normal operation of the frequency converter and extend the service life of the equipment, it is recommended to select a suitable braking resistor and correctly connect it to the frequency converter.
What size braking resistor does a 55kw inverter use?
A 55KW inverter requires a 9.1Ω or 13.6Ω braking resistor. Among them, an 8.2-ohm braking resistor is also feasible, but its braking power is about 20KW. Specific parameter selection needs to be determined based on actual working conditions and application requirements. A 55KW inverter requires a 9.1Ω or 13.6Ω braking resistor. Among them, an 8.2-ohm braking resistor is also feasible, but its braking power is about 20KW. Specific parameter selection needs to be determined based on actual working conditions and application requirements.
How to judge the quality of braking resistor?
You can judge the quality of the braking resistor through the following methods:
- Appearance observation method: First, you can observe with the naked eye whether there is any obvious damage on the appearance of the braking resistor, such as cracks, damage or deformation, etc. At the same time, you can observe whether the solder joints of the resistor are in good condition and whether they are loose or burnt. If there is obvious damage or bad solder joints, then it is most likely a bad brake resistor.
- Usage efficiency evaluation method: Usage efficiency is an important basis for evaluating the quality of the braking resistor. In practical applications, if the usage rate of the braking resistor is low, the smaller the degree of heat generation, the less energy consumed on the resistor, and the worse the braking effect. On the contrary, if the usage rate of the braking resistor is higher, the degree of heat generation is greater, and the more energy consumed on the resistor, the better the braking effect will be. Therefore, the quality of the braking resistor can be judged based on its usage rate and braking effect.
- Measurement method: If the above methods cannot determine the quality of the braking resistor, you can also use the measurement method to detect it. You can use a multimeter to measure the resistance and power of the braking resistor and compare it with the standard value to determine the quality of the braking resistor. At the same time, you can use a thermometer to measure the temperature of the braking resistor. Under normal circumstances, the operating temperature of the braking resistor should be below 80°C. If the temperature is too high, it may be caused by damage to the braking resistor or poor heat dissipation.
To sum up, judging the quality of the braking resistor can be detected and evaluated through appearance observation, efficiency evaluation and measurement.
When selecting and using a braking resistor, comprehensive considerations need to be made based on the actual situation to ensure the normal operation of the system and extend the service life of the equipment.